A new type of lamp strip molding processing method
A technology for forming and processing light strips, applied in the processing of insulating substrates/layers, printed circuits, electrical components, etc., can solve the problems of high processing costs, low production efficiency, and high processing costs of gong boards, and improve aesthetics. As well as the effect of quality, improved production efficiency, and high machining accuracy
- Summary
- Abstract
- Description
- Claims
- Application Information
AI Technical Summary
Problems solved by technology
Method used
Image
Examples
Embodiment Construction
[0027] In order to make the technical means, creative features, goals and effects achieved by the present invention easy to understand, the technical solution of the present invention will be clearly and completely described below.
[0028] Take the PNL-shaped light strip with a thickness of 1.0mm as an example, such as figure 1 As shown, the edge width of the PNL-shaped light strip is ≥8.5mm. like image 3 As shown, the V-CUT imposition spacing B=0.2mm. like figure 2 As shown, the V-CUT depth is set to 0.65mm in the design of the V-CUT cut-through section drawing, that is, the V-CUT excess thickness is set to 2.0 / 2-0.3=0.7mm, and the upper and lower knives cut into half the thickness of the light strip and then Add 0.15mm, upper knife V-CUT depth 0.65mm+lower knife V-CUT depth 0.65mm=1.3mm>board thickness 1.0mm, to ensure that the light strip can be cut through. like Figure 4 As shown, take 2 pieces of PNL-shaped light strips, hang the short sides on the PIN pins of th...
PUM
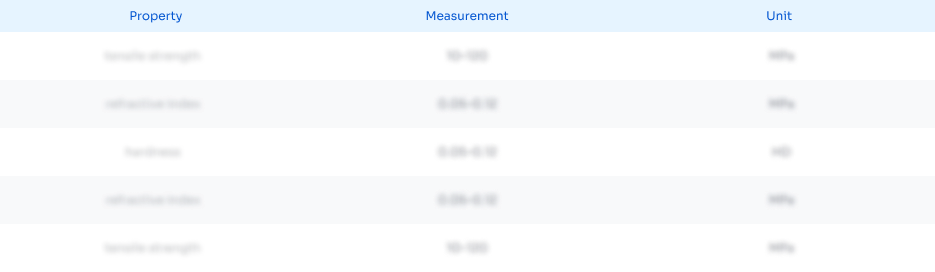
Abstract
Description
Claims
Application Information

- R&D
- Intellectual Property
- Life Sciences
- Materials
- Tech Scout
- Unparalleled Data Quality
- Higher Quality Content
- 60% Fewer Hallucinations
Browse by: Latest US Patents, China's latest patents, Technical Efficacy Thesaurus, Application Domain, Technology Topic, Popular Technical Reports.
© 2025 PatSnap. All rights reserved.Legal|Privacy policy|Modern Slavery Act Transparency Statement|Sitemap|About US| Contact US: help@patsnap.com