High elastic chlorinated polyethylene sheath material
A technology of chlorinated polyethylene and sheath materials, applied in rubber insulators, organic insulators, etc., can solve the problems of poor elasticity of chlorinated polyethylene, poor tear resistance, and rising cost of cable sheaths, and achieve excellent weather resistance , Improve resilience and reduce manufacturing cost
- Summary
- Abstract
- Description
- Claims
- Application Information
AI Technical Summary
Problems solved by technology
Method used
Examples
specific Embodiment 1
[0012] Choose 80 parts of chlorinated polyethylene rubber, 20 parts of CR / PVC co-precipitation glue, 0.5 parts of anti-aging agent RD, 1 part of paraffin wax, 3 parts of polyethylene wax, 6 parts of magnesium oxide, 1 part of lead stearate, NA-22 1.5 parts, 10 parts of high wear-resistant carbon black, 40 parts of calcined clay, 10 parts of calcium carbonate, 8 parts of antimony trioxide, 15 parts of chlorinated paraffin oil, and 12 parts of DOP. Put the above materials into the internal mixer and knead for 5~7 minutes, lift the top bolt to sweep the material, repeat twice, and then continue to knead until the temperature shows 100°C, discharge the kneaded rubber to the open kneader and turn it over for kneading, then Do not open strips, put them back into the internal mixer after cooling, add 4 parts of DCP and 2 parts of TAIC, and mix for 1 minute, then open strips and produce slices on the three-roller laminator, and put the finished product into the sulfur workshop after 16...
specific Embodiment 2
[0014] 85 parts of chlorinated polyethylene rubber, 15 parts of CR / PVC co-precipitation glue, 0.8 parts of anti-aging agent RD, 2 parts of paraffin wax, 2 parts of polyethylene wax, 8 parts of magnesium oxide, 2 parts of lead stearate, NA-22 1 13 parts of high wear-resistant carbon black, 38 parts of calcined clay, 8 parts of calcium carbonate, 6 parts of antimony trioxide, 12 parts of chlorinated paraffin oil, and 10 parts of DOP. Put the above materials into the internal mixer and knead for 5~7 minutes, lift the top bolt to sweep the material, repeat twice, and then continue to knead until the temperature shows 100°C, discharge the kneaded rubber to the open kneader and turn it over for kneading, then Do not cut strips, put them back into the internal mixer after cooling, add 3.5 parts of DCP and 3 parts of TAIC, mix for 1 minute, and carry out strips and slices on the three-roller laminator. After the finished product is placed for 16 hours, it is put into the continuous sul...
specific Embodiment 3
[0016] 90 parts of chlorinated polyethylene rubber, 10 parts of CR / PVC co-precipitation glue, 1 part of anti-aging agent RD, 3 parts of paraffin wax, 1 part of polyethylene wax, 10 parts of magnesium oxide, 3 parts of lead stearate, 0.5 part of NA-22 , 15 parts of high wear-resistant carbon black, 35 parts of calcined clay, 5 parts of calcium carbonate, 8 parts of antimony trioxide, 15 parts of chlorinated paraffin oil, and 8 parts of DOP. Put the above materials into the internal mixer and knead for 5~7 minutes, lift the top bolt to sweep the material, repeat twice, and then continue to knead until the temperature shows 100°C, discharge the kneaded rubber to the open kneader and turn it over for kneading, then Do not open strips, put them back into the internal mixer after cooling, add 3 parts of DCP and 4 parts of TAIC, and mix for 1 minute, then open strips and produce slices on a three-roller laminator, and put the finished product into the sulfur plant after 16 hours. In ...
PUM
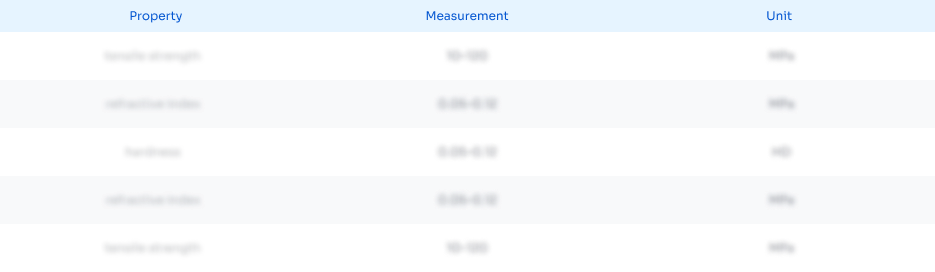
Abstract
Description
Claims
Application Information

- R&D Engineer
- R&D Manager
- IP Professional
- Industry Leading Data Capabilities
- Powerful AI technology
- Patent DNA Extraction
Browse by: Latest US Patents, China's latest patents, Technical Efficacy Thesaurus, Application Domain, Technology Topic, Popular Technical Reports.
© 2024 PatSnap. All rights reserved.Legal|Privacy policy|Modern Slavery Act Transparency Statement|Sitemap|About US| Contact US: help@patsnap.com