Preparation method of fluorine-containing phenol
A technology for fluorine-containing phenol and fluorine-containing bromobenzene is applied in the field of preparation of fluorine-containing phenol, can solve the problems of low yield of fluorine-containing phenol, harsh reaction conditions, low yield and the like, and achieves low conventional cost of raw materials and mild reaction conditions. , the effect of high yield
- Summary
- Abstract
- Description
- Claims
- Application Information
AI Technical Summary
Problems solved by technology
Method used
Image
Examples
preparation example Construction
[0033] The present invention provides a preparation method of fluorine-containing phenol, including the following steps:
[0034] a) Mix the copper catalyst, ligand, base, fluorine-containing bromobenzene and tert-butanol, and perform etherification reaction to obtain fluorine-containing phenyl tert-butyl ether;
[0035] b) Mixing the fluorine-containing phenyl tert-butyl ether obtained in step a) with concentrated sulfuric acid and water to perform a hydrolysis reaction to obtain a fluorine-containing phenol.
[0036] The present invention firstly mixes copper catalyst, ligand, base, fluorine-containing bromobenzene and tert-butanol to carry out etherification reaction to obtain fluorine-containing phenyl tert-butyl ether. In the present invention, the copper catalyst is preferably one or more of cuprous bromide, cuprous chloride and cuprous iodide, and more preferably cuprous bromide and / or cuprous iodide. The present invention has no special restrictions on the source of the copp...
Embodiment 1
[0079] (1) Set up a mechanical stirrer, a thermometer and a spherical condenser into a 2000mL three-necked flask. Under the protection of nitrogen, 7.17g cuprous bromide (0.05mol), 82.9g potassium carbonate (0.6mol), 633g tert-butanol, 10.9g1 , 10-Phen (0.055mol) and 211.0g 3,4,5-trifluorobromobenzene (1.0mol) were added to a three-necked flask, the oil bath was heated to an internal temperature of 80℃, and reacted for 5h; after the reaction, the temperature was cooled to room temperature with stirring 9.3g of cuprous bromide was recovered by suction filtration, and then 7.9g of dry solid cuprous bromide was recovered by vacuum drying; the mother liquor was concentrated under reduced pressure on a rotary evaporator to recover 566g of tert-butanol to obtain 313g of liquid-solid mixture, and then filtered to obtain 94.0 g potassium salt; then the mother liquor is subjected to vacuum distillation under a vacuum of 7 mbar, and the fraction from 66°C to 67°C is received to obtain 182...
Embodiment 2
[0085] (1) Set up a mechanical stirrer, a thermometer and a spherical condenser into a 2000mL three-necked flask. Under the protection of nitrogen, add 4.9g cuprous chloride (0.05mol), 69.1g potassium carbonate (0.5mol), 579g tert-butanol, 6.4g TMEDA (0.055mol) and 193.0g of 3,5-difluorobromobenzene (1.0mol) were added to a three-necked flask, the oil bath was heated to an internal temperature of 80°C, and reacted for 5 hours; after the reaction, the temperature was cooled to room temperature with stirring, and 9.3g was recovered by suction filtration The cuprous chloride is vacuum dried and recovered to obtain 8.2 g of dry solid cuprous chloride; the mother liquor is concentrated under reduced pressure on a rotary evaporator to recover 506 g of tert-butanol to obtain 268 g of liquid-solid mixture, which is suction filtered to obtain 86.5 g of potassium salt; The mother liquor was subjected to vacuum distillation under a vacuum of 7 mbar, and the fraction from 66°C to 67°C was r...
PUM
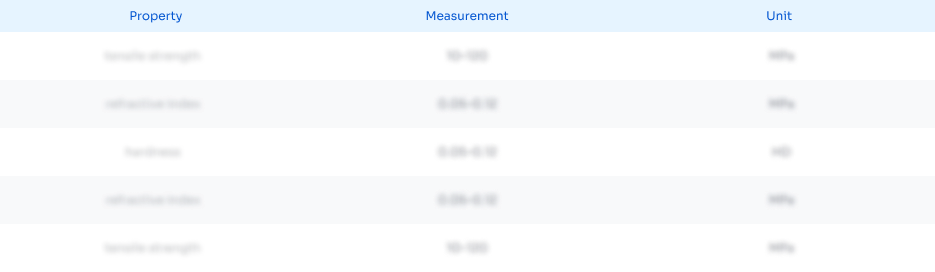
Abstract
Description
Claims
Application Information

- Generate Ideas
- Intellectual Property
- Life Sciences
- Materials
- Tech Scout
- Unparalleled Data Quality
- Higher Quality Content
- 60% Fewer Hallucinations
Browse by: Latest US Patents, China's latest patents, Technical Efficacy Thesaurus, Application Domain, Technology Topic, Popular Technical Reports.
© 2025 PatSnap. All rights reserved.Legal|Privacy policy|Modern Slavery Act Transparency Statement|Sitemap|About US| Contact US: help@patsnap.com