A method of monitoring grinding wheel wear and grinding burn by using grinding force
A technology for grinding burns and grinding forces, which is applied to the parts of grinding machine tools, grinding/polishing equipment, grinding/polishing safety devices, etc., can solve the problems of small application, and achieve the promotion of development, intelligence and The effect of automation and the avoidance of grinding burn
- Summary
- Abstract
- Description
- Claims
- Application Information
AI Technical Summary
Problems solved by technology
Method used
Image
Examples
Embodiment 1
[0054] Taking the monitoring process of microcrystalline corundum grinding wheel form grinding 20CrMnTi steel gear by using the time domain signal characteristics of grinding force as an example, the execution process is shown in the attached figure 1 As shown, it includes the following steps:
[0055] The first step: collect the discrete time series of the grinding force signal in the grinding process in real time, and obtain the grinding force signal sample set X.
[0056] (1) Clear and calibrate the dynamometer sensor in advance, so that the zero drift M is less than 2, and set the acquisition frequency of the dynamometer sensor to 1000 Hz.
[0057] (2) Use the dynamometer sensor to collect real-time data on the change of grinding force over time during the form grinding process of 20CrMnTi steel gears.
[0058] The dynamometer sensor can use the Swiss KISTLER brand 94272 model.
[0059] figure 2 In order to change the grinding force in the whole grinding process, it di...
Embodiment 2
[0081] Taking the monitoring process of microcrystalline corundum grinding wheel form grinding 20CrMnTi steel gear as an example by using the frequency domain signal characteristics of grinding force, the execution process is shown in the attached image 3 As shown, it includes the following steps:
[0082] The first step: the same as the first step in Embodiment 1, and will not be repeated here.
[0083] The second step: extract the frequency domain characteristic value of the grinding force signal from the grinding force signal sample set X obtained in the first step, and the frequency domain characteristics include: the kurtosis Xq of the amplitude spectrum waveform, the pulse index I, and the cumulative probability distribution function PF(k), and the spectral centroid Fmid of the power spectrum.
[0084](1) Perform discrete Fourier transform analysis on the discrete time series X of grinding force to obtain the amplitude spectrum and power spectrum. Among them, the ampl...
PUM
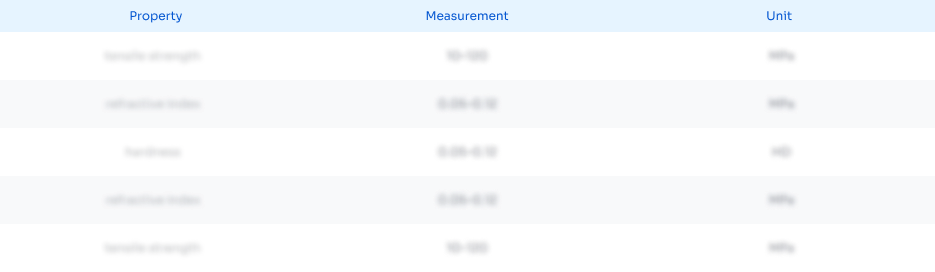
Abstract
Description
Claims
Application Information

- R&D
- Intellectual Property
- Life Sciences
- Materials
- Tech Scout
- Unparalleled Data Quality
- Higher Quality Content
- 60% Fewer Hallucinations
Browse by: Latest US Patents, China's latest patents, Technical Efficacy Thesaurus, Application Domain, Technology Topic, Popular Technical Reports.
© 2025 PatSnap. All rights reserved.Legal|Privacy policy|Modern Slavery Act Transparency Statement|Sitemap|About US| Contact US: help@patsnap.com