Interlayer fluorescent glass and preparation method and application thereof
A fluorescent glass and interlayer technology, applied in the direction of electrical components, circuits, semiconductor devices, etc., can solve the problems of affecting service life, easy aging, and easy corrosion, etc., and achieve the effects of reducing economic costs, low equipment requirements, and avoiding direct contact
- Summary
- Abstract
- Description
- Claims
- Application Information
AI Technical Summary
Problems solved by technology
Method used
Image
Examples
Embodiment 1
[0055] Such as figure 1 As shown in the figure, the Ce:YAG glass slurry 1 is printed on a φ50 glass plate 1 with a thickness of 0.4mm through a 100-mesh screen. The same operation process is used to obtain the same glass plate 2, and then the produced The obtained two glass plate samples were respectively placed in a precision annealing furnace, raised from room temperature to 200°C in 9 hours, kept at 200°C for 2 hours, then cooled to 50°C, the precision annealing furnace was closed, and the temperature was automatically lowered to The glass slurry obtained at room temperature was dried on a glass plate. Then put the two dried glass plate samples together in a sintering furnace to raise the temperature from room temperature to 550 ° C for 1 h, and keep it at 550 ° C for 10 min, and then cool down to room temperature with the furnace to obtain a Ce: YAG fluorescent layer with a thickness of Laminated glass with a thickness of 20 μm and a transmittance of more than 80% has a s...
Embodiment 2
[0059] In this embodiment, the Ce:YAG fluorescent glass slurry 1 in the embodiment 1 is replaced with the Ce:YAG fluorescent glass slurry 2, and the rest are the same as in the embodiment 1, and will not be repeated.
[0060] The Ce: YAG fluorescent glass slurry 2 is composed of: PbO: 40 parts, B 2 o 3 : 10 parts, SiO 2 : 6 parts, ZnO: 4 parts and Ce: YAG phosphor powder: 10 parts were accurately weighed, then put into an agate mortar, mixed and ground evenly, and the ground glass frit and deionized water were mixed at a mass ratio of 2.5:1. Mix and stir well to make a slurry. Then the prepared laminated glass was matched with the 3328 blue LED chip and tested, and the 3328 blue LED chip was matched and tested, and the light effect was 58.45lm / W, the color temperature was 7425K, and the color rendering index was 58.45lm / W. 76.8.
Embodiment 3
[0062] In this example, the temperature in Example 1 was raised from room temperature to 200°C in 9 hours, and kept at 200°C for 2 hours, then cooled to 50°C, the precision annealing furnace was closed, and the temperature was automatically lowered to room temperature to obtain glass The slurry was dried on a glass plate with a thickness of 1 mm. Then put the two dried glass plate samples together in a sintering furnace to raise the temperature from room temperature to 550°C for 1 hour, and keep the temperature at 550°C for 10 minutes, then change it to take 8 hours to rise from room temperature to 250°C, and Insulate at 250°C for 1 hour, then cool to 50°C, close the precision annealing furnace, automatically cool down to room temperature to obtain glass slurry and dry it on a glass plate. Then put the two dried glass plate samples together in a sintering furnace to raise the temperature from room temperature to 600 ° C for 1 h, and keep the temperature at 600 ° C for 5 min, a...
PUM
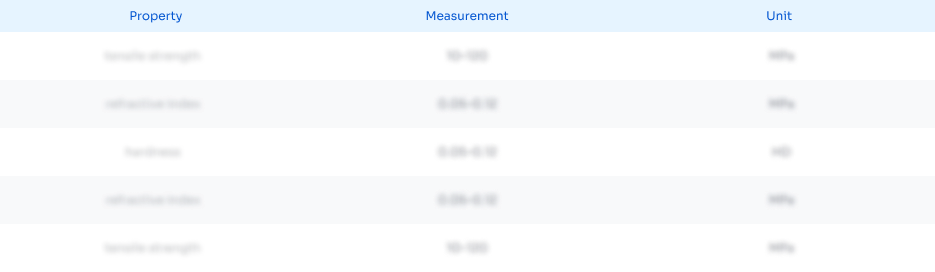
Abstract
Description
Claims
Application Information

- R&D Engineer
- R&D Manager
- IP Professional
- Industry Leading Data Capabilities
- Powerful AI technology
- Patent DNA Extraction
Browse by: Latest US Patents, China's latest patents, Technical Efficacy Thesaurus, Application Domain, Technology Topic, Popular Technical Reports.
© 2024 PatSnap. All rights reserved.Legal|Privacy policy|Modern Slavery Act Transparency Statement|Sitemap|About US| Contact US: help@patsnap.com