Heatproof environment-friendly material for preventing noise pollution and manufacturing method thereof
An environmentally friendly material and anti-noise technology, which is applied in the direction of liquid crystal materials, chemical instruments and methods, etc., can solve the problems of high toxicity of combustion products, potential safety hazards, and difficulty in molding, so as to achieve increased sound insulation effect, good sound insulation effect, and foaming The effect of a large number
- Summary
- Abstract
- Description
- Claims
- Application Information
AI Technical Summary
Problems solved by technology
Method used
Examples
Embodiment 1
[0022] A method for manufacturing a heat-resistant and environmentally-friendly material for preventing noise pollution, including the following steps:
[0023] 1) Preparation of raw materials, tooling and equipment
[0024] ① Dry the fully aromatic liquid crystal polymer to control the liquid water content to not higher than 0.02%;
[0025] ②Hydroxypropyl methyl cellulose, fluorocarbon, liquid ethylene propylene rubber and the dried liquid crystal polymer obtained in step ① are uniformly mixed to obtain a raw material mixture for use;
[0026] ③Preheat the mold to 125℃;
[0027] ④ Preheat the barrel used to contain raw materials in the equipment to 315°C;
[0028] 2) Plasticization
[0029] ①Rotate the barrel to control the speed of 130rpm;
[0030] ② Fill the raw material mixture obtained in step ② of 1) into the barrel, control the temperature of the barrel at the front section 315°C, the middle section 335°C, and the rear section 340°C, and the heating residence time in the barrel is 3...
Embodiment 2
[0037] The main body is the same as in Example 1, the differences are:
[0038] Use non-wholly aromatic liquid crystal polymer;
[0039] 1) Preparation of raw materials, tooling and equipment
[0040] ③Preheat the mold to 115℃;
[0041] ④ Preheat the barrel used to contain raw materials in the equipment to 310°C;
[0042] 2) Plasticization
[0043] ① Rotate the barrel to control the speed of 120rpm;
[0044] ② Fill the raw material mixture obtained in step ② of 1) into the barrel, control the temperature of the barrel at the front section 310°C, the middle section 330°C, and the rear section 335°C, and the heating residence time in the barrel is 35 minutes to complete the plasticization process. Obtain the compound to be injected;
[0045] 1) Among the raw materials in step ②, liquid crystal polymer accounted for 88.5%, hydroxypropyl methylcellulose accounted for 1.8%, fluorocarbon accounted for 6.2%, and liquid ethylene propylene rubber accounted for 3.5%.
Embodiment 3
[0047] The main body is the same as in Example 1, the differences are:
[0048] 1) Preparation of raw materials, tooling and equipment
[0049] ③Preheat the mold to 130°C;
[0050] ④ Preheat the barrel used to contain raw materials in the equipment to 325°C;
[0051] 2) Plasticization
[0052] ① Rotate the barrel to control the speed of 140rpm;
[0053] ② Fill the raw material mixture obtained in step ② of 1) into the barrel, control the temperature of the barrel at the front section 325°C, the middle section 340°C, and the rear section 350°C. The heating residence time in the barrel is 38 minutes, and the plasticization process is completed. Obtain the compound to be injected;
[0054] 1) Among the raw materials in step ②, liquid crystal polymer accounts for 90.5%, hydroxypropyl methylcellulose accounts for 2.5%, fluorocarbons accounts for 4.5%, and liquid ethylene propylene rubber accounts for 2.5%.
PUM
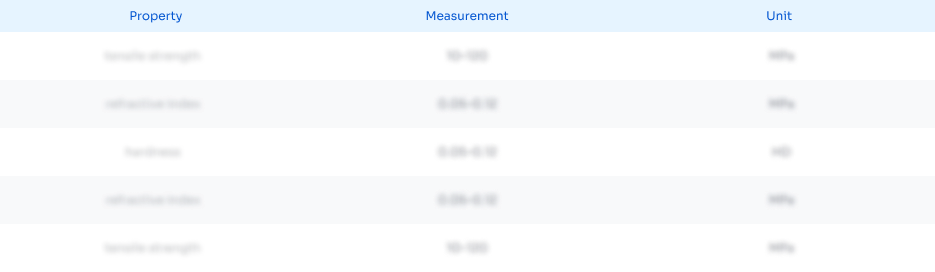
Abstract
Description
Claims
Application Information

- R&D
- Intellectual Property
- Life Sciences
- Materials
- Tech Scout
- Unparalleled Data Quality
- Higher Quality Content
- 60% Fewer Hallucinations
Browse by: Latest US Patents, China's latest patents, Technical Efficacy Thesaurus, Application Domain, Technology Topic, Popular Technical Reports.
© 2025 PatSnap. All rights reserved.Legal|Privacy policy|Modern Slavery Act Transparency Statement|Sitemap|About US| Contact US: help@patsnap.com