Method for preparing rubber vulcanization accelerator CBS by using microchannel reactor
A microchannel reactor and rubber vulcanization technology, applied in the field of fine chemical product production, can solve the problems of large influence of batch human operation factors, environmental pollution, unstable quality, etc., and achieve good industrial application prospects, high safety performance, The effect of shortened reaction time
- Summary
- Abstract
- Description
- Claims
- Application Information
AI Technical Summary
Problems solved by technology
Method used
Image
Examples
Embodiment 1
[0032] Take 1 mol of accelerator M and add 1.2 mol of cyclohexylamine to make a solution, then take 1.25 mol of hydrogen peroxide, drive the two-phase solution through the flow pump and enter the reactor with a coil diameter of 5 mm through the Y mixer. The flow rate of the microreactor is 5mL / min, the residence time of the reaction liquid in the reactor is 5min, and the reaction temperature is 40°C. After one cycle, the reaction solution was collected. The yield was determined to be 94.9%, the melting point was 99.2°C, and the appearance was off-white powder.
Embodiment 2
[0034] Take 1 mol of accelerator M and add 1.5 mol of cyclohexylamine to prepare a solution, then take 1.5 mol of hydrogen peroxide, and drive the two-phase solution through the flow pump to enter the reactor with a coil diameter of 5 mm through the Y mixer. The flow rate of the microreactor is 5mL / min, the residence time of the reaction liquid in the reactor is 5min, and the reaction temperature is 40°C. After one cycle, the reaction solution was collected. The yield was determined to be 89.2%, the melting point was 98.5°C, and the appearance was off-white powder.
Embodiment 3
[0036] Take 1 mol of accelerator M and add 1.8 mol of cyclohexylamine to prepare a solution, then take 1.5 mol of hydrogen peroxide, and drive the two-phase solution through the flow pump to enter the reactor with a coil diameter of 5 mm through the Y mixer. The flow rate of the microreactor is 10mL / min, the residence time of the reaction liquid in the reactor is 5min, and the reaction temperature is 45°C. After one cycle, the reaction solution was collected. The yield was determined to be 87.2%, the melting point was 98.5°C, and the appearance was off-white powder.
PUM
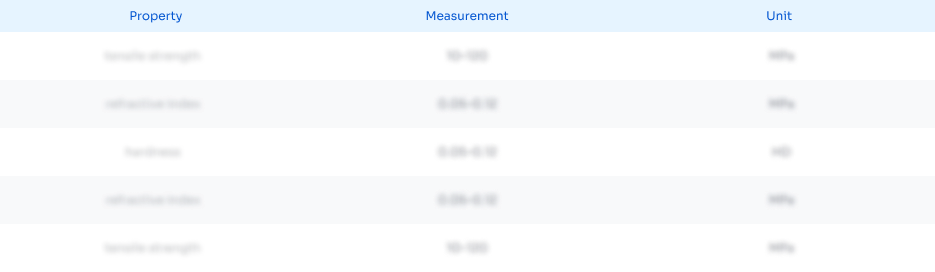
Abstract
Description
Claims
Application Information

- R&D Engineer
- R&D Manager
- IP Professional
- Industry Leading Data Capabilities
- Powerful AI technology
- Patent DNA Extraction
Browse by: Latest US Patents, China's latest patents, Technical Efficacy Thesaurus, Application Domain, Technology Topic, Popular Technical Reports.
© 2024 PatSnap. All rights reserved.Legal|Privacy policy|Modern Slavery Act Transparency Statement|Sitemap|About US| Contact US: help@patsnap.com