Method for reducing air leak rate in iron ore sintering process
A technology of sintering process and air leakage rate, applied in the field of sintering, can solve the problems of difficult processing, increased energy consumption of sintering, and reduced pollutant emission concentration, and achieves the effect of increasing temperature, reducing exhaust gas volume and improving quality
- Summary
- Abstract
- Description
- Claims
- Application Information
AI Technical Summary
Problems solved by technology
Method used
Image
Examples
Embodiment Construction
[0045] The following will clearly and completely describe the technical solutions in the embodiments of the present invention. Obviously, the described embodiments are only a small part of the present invention, rather than all the embodiments. Based on the embodiments of the present invention, all other embodiments obtained by persons of ordinary skill in the art without making creative efforts belong to the present invention.
[0046] Taking a steel sintering machine as an example,
[0047] Use the standard gas to calibrate the flue gas analyzer, and the technical indicators of the flue gas analyzer are shown in Table 1 below. The flue gas flow rate and SO 2 For the concentration, the existing test hole can be used or the hole can be re-opened. After the hole is opened, the bolt can be tightened to seal it, which is convenient for re-measurement next time.
[0048] Table 1 Technical indicators of flue gas analyzer
[0049]
[0050] (a) Before the sintering flue to the ...
PUM
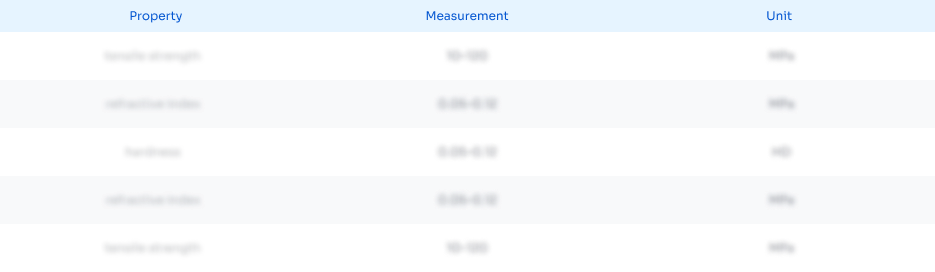
Abstract
Description
Claims
Application Information

- R&D
- Intellectual Property
- Life Sciences
- Materials
- Tech Scout
- Unparalleled Data Quality
- Higher Quality Content
- 60% Fewer Hallucinations
Browse by: Latest US Patents, China's latest patents, Technical Efficacy Thesaurus, Application Domain, Technology Topic, Popular Technical Reports.
© 2025 PatSnap. All rights reserved.Legal|Privacy policy|Modern Slavery Act Transparency Statement|Sitemap|About US| Contact US: help@patsnap.com