Method for realizing deep depletion on copper slag through multielement gas substep injection
A gas and multi-component technology, applied in the field of metallurgy, can solve the problems of high element content, high grinding cost, reduce copper content in molten iron, etc., and achieve the effect of high alloy copper content, less reducing agent consumption and less flux addition.
- Summary
- Abstract
- Description
- Claims
- Application Information
AI Technical Summary
Problems solved by technology
Method used
Image
Examples
Embodiment 1
[0077] Heat 200kg of copper slag 1 in the submerged arc electric furnace to the general molten copper slag temperature of 1250°C, continue to heat up to 1450°C to 1500°C, insert the lowering lance into the molten pool, and spray oxidizing gas 1 (air) for 30 minutes. 40.0Nm 3 / h. After the gasification desulfurization process is completed, the injection gas source is switched to reducing gas 1 (natural gas), and the injection is continued for 30 minutes, and the injection flow rate is 20.0Nm 3 / h, after the reduction, settling for 10 minutes, the copper-iron alloy melt appeared in the molten pool, and the alloy liquid was released from the bottom of the furnace.
[0078] The obtained alloy is 16.0kg, which contains 53.0% copper, 0.43% copper in the depleted tailings, less than 0.01% sulfur, and a copper recovery rate of 92.2%.
Embodiment 2
[0080] Heat 200kg of copper slag 1 in the submerged arc electric furnace to the general molten copper slag temperature of 1250°C, continue heating to 1450°C to 1500°C, insert the lowering lance into the molten pool, and spray oxidizing gas 1 (air) for 50 minutes (the first 30 minutes to spray The blowing flow is 30.0Nm 3 / h, the injection flow rate is 15Nm in the last 20min 3 / h). After the gasification desulfurization process is completed, the injection gas source is switched to reducing gas 1 (natural gas), and the injection continues for 60 minutes, with an injection flow rate of 20.0Nm 3 / h, after the reduction, settling for 10 minutes, the copper-iron alloy melt appeared in the molten pool, and the alloy liquid was released from the bottom of the furnace.
[0081] The obtained alloy is 37.4kg, which contains 23.4% copper, 0.31% copper in the depleted tailings, less than 0.01% sulfur, and a copper recovery rate of 95.2%.
Embodiment 3
[0083]Heat 200kg of copper slag 1 in the submerged arc electric furnace to the general molten copper slag temperature of 1250°C, continue to heat up to 1450°C to 1500°C, insert the lowering lance into the molten pool, and spray oxidizing gas 2 (oxygen) for 10 minutes. 20.0Nm 3 / h; the gas source is switched to gas 1 (air) injection for 20 minutes, and the injection flow rate is 25Nm 3 / h. After the gasification desulfurization process is completed, the injection gas source is switched to reducing gas 3, and the injection is continued for 60 minutes, and the injection flow rate is 50.0Nm 3 / h, after the reduction, settling for 10 minutes, the copper-iron alloy melt appeared in the molten pool, and the alloy liquid was released from the bottom of the furnace.
[0084] The obtained alloy is 10.8kg, which contains 76.7% copper, 0.50% copper and less than 0.01% sulfur in the depleted tailings, and the copper recovery rate is 90.4%.
PUM
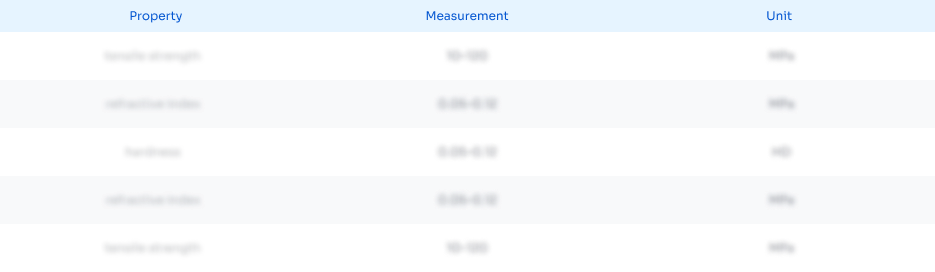
Abstract
Description
Claims
Application Information

- Generate Ideas
- Intellectual Property
- Life Sciences
- Materials
- Tech Scout
- Unparalleled Data Quality
- Higher Quality Content
- 60% Fewer Hallucinations
Browse by: Latest US Patents, China's latest patents, Technical Efficacy Thesaurus, Application Domain, Technology Topic, Popular Technical Reports.
© 2025 PatSnap. All rights reserved.Legal|Privacy policy|Modern Slavery Act Transparency Statement|Sitemap|About US| Contact US: help@patsnap.com