Preparation method of microcrystalline cellulose
A technology of microcrystalline cellulose and pulp, which is applied in the direction of pulping with inorganic alkali, can solve the problems of many impurities, improvement of product quality, unfavorable microcrystalline cellulose, etc., and achieve the effect of increasing raw material sources and improving quality
- Summary
- Abstract
- Description
- Claims
- Application Information
AI Technical Summary
Problems solved by technology
Method used
Examples
preparation example Construction
[0024] A preparation method of microcrystalline cellulose, comprising the following steps:
[0025] Pretreatment of chemical pulp sheet: disperse the pulp sheet in water, configure it into a pulp suspension with a mass fraction of 0.1%-15%, soak it for 12-72h to make it swell, and then react it in the reactor to obtain slurry;
[0026] Wherein, the commercial chemical pulp board is at least one of coniferous wood pulp board, hardwood pulp board and bamboo pulp board.
[0027] Further, the α-cellulose content of the commercial chemical pulp board is 60%-90%, and the average degree of polymerization is 700-1400.
[0028] Further, in the pretreatment step of the chemical pulp board, the temperature of the reactor is 160°C-200°C, and the reaction time in the reactor is 2-60min.
[0029] Alkali treatment of slurry: Separating the solid and liquid of the slurry obtained after pretreatment, washing the obtained solid slurry with water to neutrality and then treating it with lye; in ...
Embodiment 1
[0037] (1) Disperse the commercial bamboo pulp board in water, configure it into a 0.1% pulp suspension, and soak it for 24 hours to make it fully swell. Place the prepared pulp suspension in a high-temperature reaction kettle and treat it at 180°C for 15 minutes to make it fully react.
[0038] (2) Separating the treated slurry from solid to liquid, and washing the obtained solid slurry with clear water to neutrality, the mass fraction of the washed slurry is 5% potassium hydroxide solution at 60°C and 10% slurry The concentration was treated for 5 minutes.
[0039] (3) The alkali-treated slurry is washed with clear water to neutrality, and then treated with 3mol / L hydrochloric acid: sulfuric acid molar ratio 1:1 mixed acid solution at 65°C for 30 minutes to fully hydrolyze it to obtain Blend containing microcrystalline cellulose.
[0040] (4) The mixture was separated from solid and liquid, washed with water until neutral, and dried in a vacuum oven at 0.08 MPa and 70° C. ...
Embodiment 2
[0043] (1) Disperse the commercial coniferous wood pulp plate in water, configure it into a 1% pulp suspension, and soak it for 36 hours to make it fully swell. Put the configured pulp suspension in a high-temperature reaction kettle, and treat it at 190°C for 30 minutes to make it fully react.
[0044] (2) Separating the treated slurry from solid to liquid, and washing the obtained solid slurry with clear water to neutrality, the mass fraction of the washed slurry is 15% sodium hydroxide solution at 50°C and 20% slurry The concentration was treated for 50 minutes.
[0045] (3) The alkali-treated slurry was washed with water to neutrality, and then treated with 1 mol / L sulfuric acid at 75° C. for 20 minutes to fully hydrolyze it, thereby obtaining a mixture containing microcrystalline cellulose.
[0046] (4) The mixture was separated into solid and liquid, washed with water until neutral, and dried in a vacuum oven at 0.085 MPa and 60° C. for 6 hours. Thereafter, the obtaine...
PUM
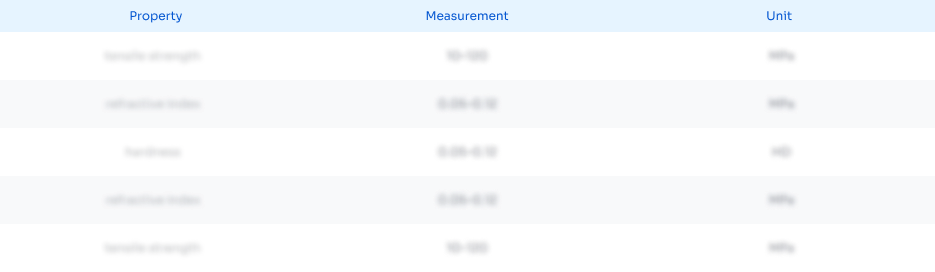
Abstract
Description
Claims
Application Information

- R&D
- Intellectual Property
- Life Sciences
- Materials
- Tech Scout
- Unparalleled Data Quality
- Higher Quality Content
- 60% Fewer Hallucinations
Browse by: Latest US Patents, China's latest patents, Technical Efficacy Thesaurus, Application Domain, Technology Topic, Popular Technical Reports.
© 2025 PatSnap. All rights reserved.Legal|Privacy policy|Modern Slavery Act Transparency Statement|Sitemap|About US| Contact US: help@patsnap.com