Error observer-based feedforward control method of fast mirror
A feedforward control and feedforward controller technology, applied in the field of fast mirror feedforward control based on error observer, can solve the problems of large target speed prediction error, poor use effect, complex structure, etc., and achieve a small amount of calculation. , the use of a wide range, the effect of simplifying the control process
- Summary
- Abstract
- Description
- Claims
- Application Information
AI Technical Summary
Problems solved by technology
Method used
Image
Examples
Embodiment Construction
[0023] The specific implementation manners of the present invention will be described in detail below in conjunction with the accompanying drawings.
[0024] as attached figure 1 Shown is a control block diagram of a fast mirror feed-forward control method based on an error observer, which includes a high-bandwidth eddy current inner loop, a CCD position outer loop, and an error observer. The core idea of this method is to use the visual axis error provided by the CCD and the output of the position loop controller to fuse to realize a high-gain observer to realize the observation and estimation of the target position, and then realize the feedforward of the target position control to reduce its CCD tracking error. The specific implementation steps of adopting described device to realize feed-forward control method are as follows:
[0025] Step (1): Install an eddy current position sensor in the fast mirror tracking control system to measure the deflection angle position of...
PUM
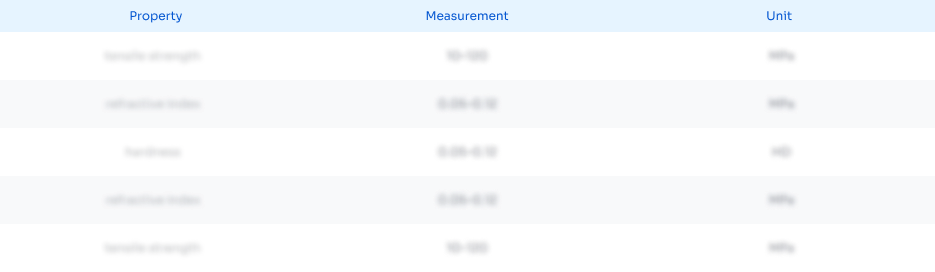
Abstract
Description
Claims
Application Information

- Generate Ideas
- Intellectual Property
- Life Sciences
- Materials
- Tech Scout
- Unparalleled Data Quality
- Higher Quality Content
- 60% Fewer Hallucinations
Browse by: Latest US Patents, China's latest patents, Technical Efficacy Thesaurus, Application Domain, Technology Topic, Popular Technical Reports.
© 2025 PatSnap. All rights reserved.Legal|Privacy policy|Modern Slavery Act Transparency Statement|Sitemap|About US| Contact US: help@patsnap.com