Resin for polyurethane sole, preparation method and application
A polyurethane resin and polyurethane technology are applied in the fields of polyurethane sole resin and preparation and application, which can solve the problem of high production cost and achieve the effects of low cost, wide adjustable range and suitable for continuous production operation.
- Summary
- Abstract
- Description
- Claims
- Application Information
AI Technical Summary
Problems solved by technology
Method used
Image
Examples
Embodiment 1
[0052] 80.0kg of polyethylene adipate diethylene glycol diol (number average molecular weight is 1000), 80.0kg of polyoxyethylene-oxypropylene glycol (number average molecular weight is 6000), 40.0kg of styrene Graft copolymerized oxyethylene-propylene oxide trihydric alcohol (the number average molecular weight is 6000), the ethylene glycol of 4.00kg, the 1,4-butanediol of 6.00kg, the ethylene glycol solution of the triethylenediamine of 0.50kg, 1.50kg of 70wt% bis(dimethylaminoethyl)ether and 30wt% dipropylene glycol solution, 0.20kg water and 0.60kg organic silicon foam stabilizer were reacted at 50°C for 2.5h, then cooled to 40°C °C, mixed for 1.5h to obtain component A of polyurethane resin.
[0053] With the diphenylmethane diisocyanate of 45.7g, the carbodiimide modified diphenylmethane diisocyanate of 15.2kg, the polyethylene adipate diethylene glycol ester diol of 7.44kg (the number average molecular weight is 1000 ) and 0.0012kg of phosphoric acid were reacted at 65...
Embodiment 2
[0057] 80.0kg of polyethylene adipate diethylene glycol diol (number average molecular weight is 1000), 80.0kg of polyoxyethylene-oxypropylene glycol (number average molecular weight is 6000), 40.0kg of styrene Graft copolymerized oxyethylene-propylene oxide trihydric alcohol (the number average molecular weight is 6000), the ethylene glycol of 4.00kg, the 1,4-butanediol of 6.00kg, the ethylene glycol solution of the triethylenediamine of 0.50kg, 1.50kg of 70wt% bis(dimethylaminoethyl)ether and 30wt% dipropylene glycol solution, 0.20kg water and 0.60kg organic silicon foam stabilizer were reacted at 50°C for 2.5h, then cooled to 40°C °C, mixed for 1.5h to obtain component A of polyurethane resin.
[0058] With the diphenylmethane diisocyanate of 4.81kg, the carbodiimide modified diphenylmethane diisocyanate of 1.61kg, the polyethylene adipate diethylene glycol diol of 1.28kg (the number average molecular weight is 1000 ) and 0.00008kg of phosphoric acid were reacted at 65°C f...
Embodiment 3
[0062] 50kg of polyethylene adipate diethylene glycol (number average molecular weight is 2000), 50.0kg of polyoxyethylene-oxypropylene glycol (number average molecular weight is 8000), 100.0kg of styrene Branch copolymerized ethylene oxide-propylene oxide trihydric alcohol (the number average molecular weight is 8000), the ethylene glycol of 10.4kg, the 1,4-butanediol of 9.60kg, the ethylene glycol solution of the triethylenediamine of 1.50kg, 1.50 A solution made of 70wt% bis(dimethylaminoethyl)ether and 30wt% dipropylene glycol, 1.00kg water and 1.40kg silicone foam stabilizer reacted at 60°C for 1.5h, then cooled to 45°C , mixed for 1.0h to obtain the polyurethane resin component A.
[0063] React 17.0kg of diphenylmethane diisocyanate, 6.82kg of polyethylene adipate diethylene glycol (number average molecular weight: 2000) and 0.0024kg of phosphoric acid at 75°C for 2 hours to obtain polyurethane resin B1 component.
[0064] React 85.2kg of diphenylmethane diisocyanate,...
PUM
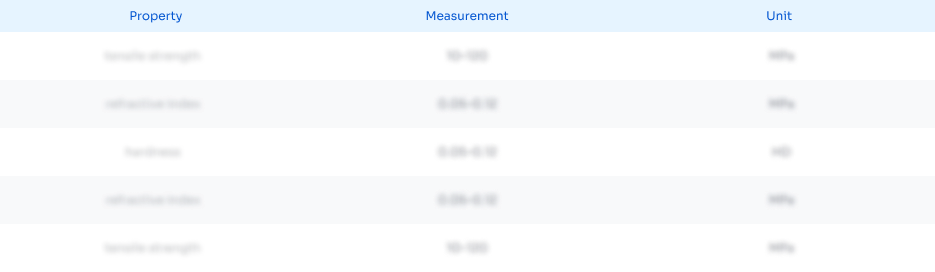
Abstract
Description
Claims
Application Information

- R&D
- Intellectual Property
- Life Sciences
- Materials
- Tech Scout
- Unparalleled Data Quality
- Higher Quality Content
- 60% Fewer Hallucinations
Browse by: Latest US Patents, China's latest patents, Technical Efficacy Thesaurus, Application Domain, Technology Topic, Popular Technical Reports.
© 2025 PatSnap. All rights reserved.Legal|Privacy policy|Modern Slavery Act Transparency Statement|Sitemap|About US| Contact US: help@patsnap.com