Treating method for residual liquid and slag slurry produced in polysilicon production
A processing method and polysilicon technology, applied in the directions of halogenated silanes, halogenated silicon compounds, etc., can solve the problem of low economical efficiency, and achieve the effect of improving economical efficiency and reducing emissions
- Summary
- Abstract
- Description
- Claims
- Application Information
AI Technical Summary
Problems solved by technology
Method used
Image
Examples
Embodiment 1
[0030] This embodiment provides a treatment method for raffinate and slag in polysilicon production. The raffinate and slag contain silicon and silicon tetrachloride. The method includes the steps of: a) feeding the raffinate and slag A catalyst is added into the slurry to make the silicon react with the silicon tetrachloride to generate hexachlorodisilane.
[0031] The method for treating the raffinate and slurry in the production of polysilicon in this embodiment increases the content of hexachlorodisilane in the raffinate and slurry through the synthesis reaction of hexachlorodisilane, and obtains raffinate and slurry with high added value. Slurry improves the economics of the hexachlorodisilane recovery process; the solid waste and liquid waste in polysilicon production are rationally converted and recycled at the same time, which reduces the cost of raffinate and slurry treatment while achieving high additional Recycling of valuable products; solve the bottleneck problem ...
Embodiment 2
[0033] like figure 1 As shown, this embodiment provides a treatment method for raffinate and slag in polysilicon production. The raffinate and slag contain silicon and silicon tetrachloride. Specifically, the raffinate and slag in this embodiment The main composition of the slurry material is 1.7wt% of trichlorosilane, 64.9wt% of silicon tetrachloride, 11.0wt% of hexachlorodisilane, 12wt% of silicon powder, and the remaining components are metal chlorides, organochlorosilanes , high boiling silicone oil, etc. The method comprises the steps of: a) adding a catalytic amount of catalyst to the raffinate and slurry in the stirred tank reactor 1 under protective gas nitrogen, and the molar ratio of the catalyst to the silicon tetrachloride is 1:500, the catalyst is a copper complex [Cu(C 12 h 8 ) 2 ] BF 4 , making the silicon and the silicon tetrachloride react at 100°C for 6 hours to generate hexachlorodisilane, wherein the hexachlorodisilane in the raffinate and slurry after...
Embodiment 3
[0050] This embodiment provides a treatment method for raffinate and slurry in polysilicon production. The raffinate and slurry contain silicon and silicon tetrachloride. Specifically, the raffinate and slurry materials in this embodiment are The main composition is 1.3wt% of trichlorosilane, 40.0wt% of silicon tetrachloride, 13.3wt% of hexachlorodisilane, 14.1wt% of silicon powder, and the remaining components are metal chloride, organochlorosilane, high Boiling silicon oil, etc., the method comprises the steps: a) under protective gas nitrogen, add a catalytic amount of catalyst to the raffinate and slurry in the stirred tank reactor, the catalyst and the silicon tetrachloride The molar ratio is 1:200, the catalyst is copper complex {Cu[(Ph) 2 PCH 2 CH 2 CH 2 P(Ph) 2 ] 2}Cl and {Cu[P(Ph) 3 ] 3}Cl mixture (mass ratio 1:1), so that the silicon and the silicon tetrachloride were reacted for 18 hours at 250° C. to generate hexachlorodisilane, wherein the residue after the...
PUM
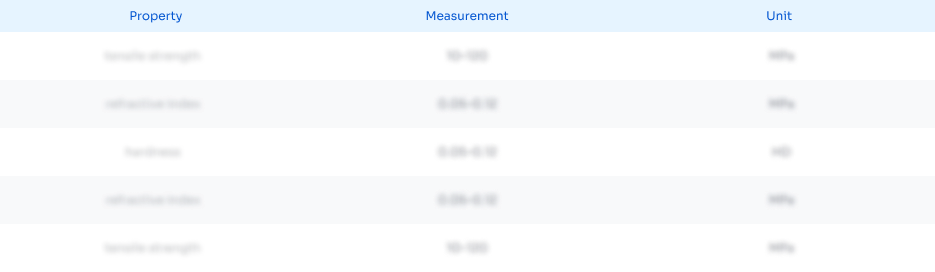
Abstract
Description
Claims
Application Information

- R&D
- Intellectual Property
- Life Sciences
- Materials
- Tech Scout
- Unparalleled Data Quality
- Higher Quality Content
- 60% Fewer Hallucinations
Browse by: Latest US Patents, China's latest patents, Technical Efficacy Thesaurus, Application Domain, Technology Topic, Popular Technical Reports.
© 2025 PatSnap. All rights reserved.Legal|Privacy policy|Modern Slavery Act Transparency Statement|Sitemap|About US| Contact US: help@patsnap.com