Manufacturing method for pattern in stepped groove
A processing method and technology of stepped grooves, which are applied in printed circuit manufacturing, electrical components, printed circuits, etc., can solve the problems of uneven copper surface, cumbersome production, and time-consuming, so as to ensure completeness, simplify the production process, and improve the pass rate. and on-time delivery
- Summary
- Abstract
- Description
- Claims
- Application Information
AI Technical Summary
Problems solved by technology
Method used
Image
Examples
Embodiment
[0033] Such as Figure 1-8 As shown, a processing method for making a pattern in a stepped groove is characterized in that the pattern in the groove is processed by laser milling to ensure the integrity of the pattern in the groove.
[0034] The specific steps of the method are as follows: 1) lamination of inner layer graphics; 2) drilling; 3) reverse milling grooves to expose inner layer graphics; 4) hole making; 5) laser cutting graphics; 6) tin plating; 7) etching; 8) Strip tin.
[0035] The tin-plated area is larger than the pattern and the hole area, and is used to protect the pattern and the hole area. The tinned area is a rectangular area. The laser cutting graphic adopts a fully automatic laser cutting machine.
PUM
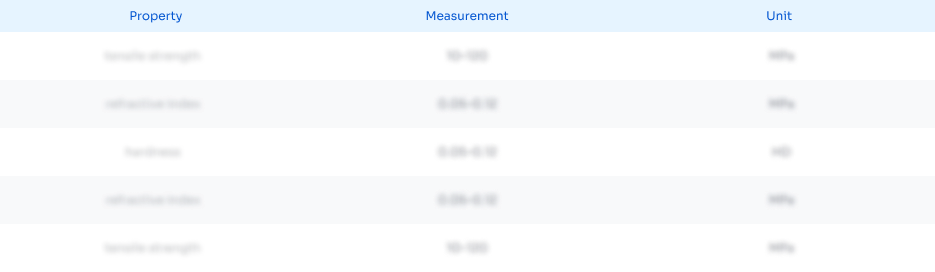
Abstract
Description
Claims
Application Information

- Generate Ideas
- Intellectual Property
- Life Sciences
- Materials
- Tech Scout
- Unparalleled Data Quality
- Higher Quality Content
- 60% Fewer Hallucinations
Browse by: Latest US Patents, China's latest patents, Technical Efficacy Thesaurus, Application Domain, Technology Topic, Popular Technical Reports.
© 2025 PatSnap. All rights reserved.Legal|Privacy policy|Modern Slavery Act Transparency Statement|Sitemap|About US| Contact US: help@patsnap.com