High-molecular polymerization reinforced plastic and preparation method thereof
A technology of polymer polymerization and reinforced plastics, which is applied in the field of new materials, can solve the problems of lack of access, and achieve the effect of high strength
- Summary
- Abstract
- Description
- Claims
- Application Information
AI Technical Summary
Problems solved by technology
Method used
Image
Examples
Embodiment 1
[0021] A polymer reinforced plastic, made of the following materials by weight, including 120 parts of polyvinyl chloride resin, 80 parts of phenolic resin, 80 parts of epoxy resin, and 60 parts of wood powder , 20 parts of glass fiber, 16 parts of diatomaceous earth, 15 parts of asbestos fiber, 10 parts of tar stone powder, 11 parts of fiber rag, 8 parts of antimony trioxide, 16 parts of graphite, 30 parts of dioctyl phthalate, hard 7 parts of hydrochloric acid salt and 7 parts of organotin.
[0022] A preparation method for polymerized reinforced plastics, comprising the following steps:
[0023] 1) Put 120 parts of polyvinyl chloride resin, 80 parts of phenolic resin and 80 parts of epoxy resin into a melting furnace, and heat it to 320°C, so that the polyvinyl chloride resin, phenolic resin and epoxy resin are melted rapidly at high temperature, and the Get mixed glue, set aside;
[0024] 2) Add 30 parts of dioctyl phthalate, 7 parts of stearate and 7 parts of organotin ...
Embodiment 2
[0031] A polymer reinforced plastic, made of the following materials in parts by weight, including 90 parts of polyvinyl chloride resin, 100 parts of phenolic resin, 100 parts of epoxy resin, 80 parts of wood flour, 36 parts of glass fiber, and 28 parts of diatomaceous earth 25 parts of asbestos fiber, 20 parts of tar stone powder, 19 parts of fiber rags, 14 parts of antimony trioxide, 20 parts of graphite, 40 parts of dioctyl phthalate, 9 parts of hard acid salt and 9 parts of organic tin .
[0032] A preparation method for polymerized reinforced plastics, comprising the following steps:
[0033] 1) Take 90 parts of polyvinyl chloride resin, 100 parts of phenolic resin and 100 parts of epoxy resin and put them into a furnace, and heat them to 400°C, so that the polyvinyl chloride resin, phenolic resin and epoxy resin are melted rapidly at high temperature. Get mixed glue, set aside;
[0034] 2) Add 40 parts of dioctyl phthalate, 9 parts of stearate and 9 parts of organic ti...
Embodiment 3
[0041] A polymer reinforced plastic, made of the following materials in parts by weight, including 105 parts of polyvinyl chloride resin, 90 parts of phenolic resin, 90 parts of epoxy resin, 70 parts of wood powder, 28 parts of glass fiber, and 22 parts of diatomaceous earth 20 parts of asbestos fiber, 15 parts of tar stone powder, 15 parts of fiber rag, 11 parts of antimony trioxide, 18 parts of graphite, 35 parts of dioctyl phthalate, 8 parts of hard acid salt and 8 parts of organic tin .
[0042] A preparation method for polymerized reinforced plastics, comprising the following steps:
[0043] 1) Put 105 parts of polyvinyl chloride resin, 90 parts of phenolic resin and 90 parts of epoxy resin into a melting furnace, and heat it to 360°C, so that the polyvinyl chloride resin, phenolic resin and epoxy resin are melted rapidly at high temperature, and the Get mixed glue, set aside;
[0044] 2) Add 35 parts of dioctyl phthalate, 8 parts of stearate and 8 parts of organic tin ...
PUM
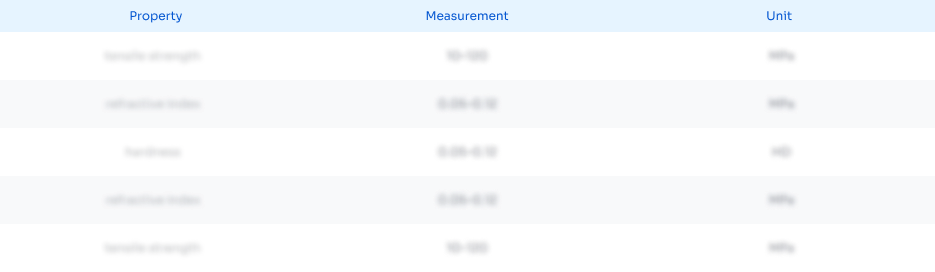
Abstract
Description
Claims
Application Information

- R&D
- Intellectual Property
- Life Sciences
- Materials
- Tech Scout
- Unparalleled Data Quality
- Higher Quality Content
- 60% Fewer Hallucinations
Browse by: Latest US Patents, China's latest patents, Technical Efficacy Thesaurus, Application Domain, Technology Topic, Popular Technical Reports.
© 2025 PatSnap. All rights reserved.Legal|Privacy policy|Modern Slavery Act Transparency Statement|Sitemap|About US| Contact US: help@patsnap.com