MCM-22/ZSM-22 composite molecular sieve catalyst and its preparation method and application
A MCM-22, composite molecular sieve technology, applied in molecular sieve catalysts, physical/chemical process catalysts, chemical instruments and methods, etc., can solve problems such as increasing the difficulty of operation, prolonging the process flow, increasing investment costs, etc., to improve isomerization. Selectivity, reducing the effect of cracking reactions
- Summary
- Abstract
- Description
- Claims
- Application Information
AI Technical Summary
Problems solved by technology
Method used
Image
Examples
Embodiment 1
[0027] 4.26g NaAlO 2 Mix evenly with 19.08g of sodium hydroxide solution in a 500ml stainless steel reaction kettle, add 33g of silica gel, 408.2g of deionized water, 18.96g of hexamethyleneimine (HMI) into the kettle in turn under stirring, and then add 1.65g CH 3 1, finally add 55g ZSM-22 again. After continuing to stir for 10 minutes, the reaction vessel was sealed and crystallized at 120° C. for 15 hours. After the crystallization was completed, a solid product (MCM-22 / ZSM-22) was isolated, and the weight content of MCM-22 was 25.4%.
[0028] Take 5.5g of tetraethyl orthosilicate, prepare 150g of methanol solution of tetraethyl orthosilicate, take 100g of the above-mentioned MCM-22 / ZSM-22 molecular sieve, dip it into the above solution for 6.5 hours, and then pass through 100% high temperature Steam treatment, the specific conditions are as follows: treatment pressure 1.0MPa, treatment temperature 350°C, treatment time 3.5 hours. Get SiO 2 Modified MCM-22 / ZSM-22 compo...
Embodiment 2
[0030] 1.488g NaAlO 2 Mix evenly with 36.06g sodium hydroxide solution in a 500ml stainless steel reaction kettle, mix 23g silica gel, 3.3gCHCl under stirring 3 、 Add 359.3g deionized water and 3.00g HMI to the kettle in turn, and finally add 100g ZSM-22. After continuing to stir for 10 minutes, the reaction vessel was sealed and crystallized at 130° C. for 20 h. After the crystallization, the solid product (MCM-22 / ZSM-22) was isolated, and the weight content of MCM-22 was 11.1%.
[0031] Take 16.8g of tetraethyl orthosilicate, prepare 150g of methanol solution of tetraethyl orthosilicate, take 100g of the above-mentioned MCM-22 / ZSM-22 molecular sieve, soak it in the above solution for 2.5 hours, and then pass through 100% high temperature Steam treatment, the specific conditions are as follows: treatment pressure 1.5MPa, treatment temperature 350°C, treatment time 2.0 hours. Get SiO 2 Modified MCM-22 / ZSM-22 composite molecular sieve with a loading capacity of 4.8%, numbe...
Embodiment 3
[0033] 1.136g NaAlO 2 Mix evenly with 24.04g of sodium hydroxide solution in a 500ml stainless steel reaction kettle, add 22g of silica gel, 237g of deionized water, 12g of HMI and 6g of cyclohexane into the kettle in sequence while stirring, and finally add 120g of ZSM-22. After continuing to stir for 10 minutes, the reaction vessel was sealed and crystallized at 120° C. for 15 hours. After the crystallization was completed, a solid product (MCM-22 / ZSM-22) was isolated, numbered S-3, and the weight content of MCM-22 was 7.5%.
[0034] Take 10.8g of tetraethyl orthosilicate, prepare 150g of methanol solution of tetraethyl orthosilicate, take 100g of the above-mentioned MCM-22 / ZSM-22 molecular sieve, soak it in the above solution for 6.5 hours, and then pass through 100% high temperature Steam treatment, the specific conditions are as follows: treatment pressure 1.5MPa, treatment temperature 350°C, treatment time 4.0 hours. Get SiO 2 Modified MCM-22 / ZSM-22 composite molecula...
PUM
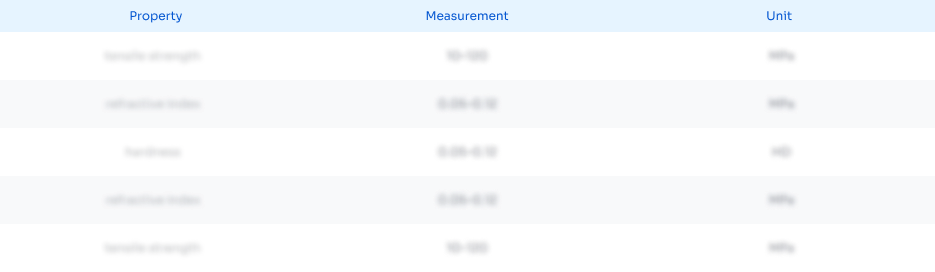
Abstract
Description
Claims
Application Information

- R&D
- Intellectual Property
- Life Sciences
- Materials
- Tech Scout
- Unparalleled Data Quality
- Higher Quality Content
- 60% Fewer Hallucinations
Browse by: Latest US Patents, China's latest patents, Technical Efficacy Thesaurus, Application Domain, Technology Topic, Popular Technical Reports.
© 2025 PatSnap. All rights reserved.Legal|Privacy policy|Modern Slavery Act Transparency Statement|Sitemap|About US| Contact US: help@patsnap.com