A dual-slag process for smelting ultra-low phosphorus and low-carbon steel in a double-blown converter
A converter smelting, ultra-low phosphorus technology, applied in the manufacture of converters, etc., can solve the problems of short smelting cycle, high requirements for supporting process equipment, etc., and achieve the effect of convenient production control, less investment and stable effect
- Summary
- Abstract
- Description
- Claims
- Application Information
AI Technical Summary
Problems solved by technology
Method used
Examples
Embodiment 1
[0017] This embodiment is a dual-slag process for smelting ultra-low phosphorus and low-carbon steel in a double-blown converter. The specific process is: add 90 tons of molten iron and 10.2 tons of scrap steel to a 100-ton double-blown converter. The conditions of the molten iron are: 4.49%C, 0.38 %Si, 0.17%Mn, 0.109%P, 0.01%S, temperature 1297°C: 20000 Nm in the first stage 3 / h of oxygen supply is turned on, and the flow rate is adjusted to 13000Nm after 1min 3 / h blowing to slag dumping. The opening position of the blowing gun is 1800mm, and after 1 minute, the opening position of the blowing gun is slowly reduced to 1300mm, and then the constant gun position is kept until the slag is dumped. Add 3148kg of lime, 2432 ore, 500kg of magnesium balls and 0.1 Nm of bottom blowing nitrogen into the converter after blowing is started 3 / min / t. After 8.5 minutes of blowing, the gun was lifted and the slag was dumped. The temperature and composition of molten iron at the end of...
Embodiment 2
[0019] This embodiment is a dual-slag process for smelting ultra-low phosphorus and low-carbon steel in a double-blown converter. The specific process is: add 88 tons of molten iron and 10.8 tons of scrap steel to a 100-ton double-blown converter. The molten iron conditions are: 4.39%C, 0.40 %Si, 0.15%Mn, 0.106%P, 0.02%S, temperature 1324°C: 20000Nm used in the first stage 3 / h oxygen supply blowing, the opening position of the blowing gun is 1850mm, and then slowly from the opening position of the blowing gun to 1300mm and keep the constant gun position, add 3150kg of lime, 2348kg of ore, 505kg of magnesium balls, bottom Nitrogen blowing intensity 0.1 Nm 3 / min / t, the temperature and composition of molten iron at the end of the first stage: 2.85%C, 0.02%Si, 0.03%Mn, 0.033%P, 0.024%S, the temperature is 1387℃; the second stage uses 18000Nm 3 For blowing with oxygen supply per hour, the opening position of the blowing gun is 1750mm, the position of the process gun can be adjus...
PUM
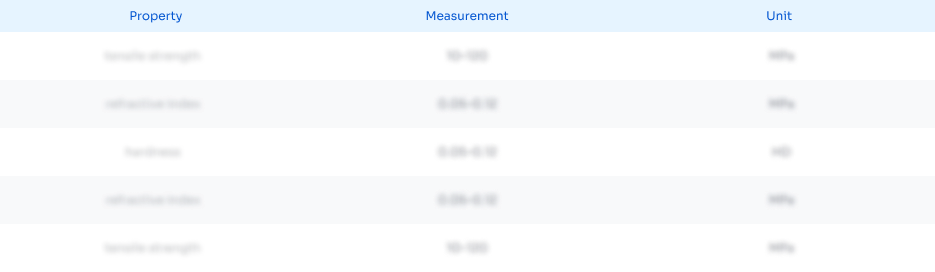
Abstract
Description
Claims
Application Information

- Generate Ideas
- Intellectual Property
- Life Sciences
- Materials
- Tech Scout
- Unparalleled Data Quality
- Higher Quality Content
- 60% Fewer Hallucinations
Browse by: Latest US Patents, China's latest patents, Technical Efficacy Thesaurus, Application Domain, Technology Topic, Popular Technical Reports.
© 2025 PatSnap. All rights reserved.Legal|Privacy policy|Modern Slavery Act Transparency Statement|Sitemap|About US| Contact US: help@patsnap.com