Laser welding quality monitoring device
A technology of laser welding quality and monitoring device, applied in laser welding equipment, welding equipment, metal processing equipment, etc., can solve the problems of slow welding speed, unsuitable for high-speed production, and high cost
- Summary
- Abstract
- Description
- Claims
- Application Information
AI Technical Summary
Problems solved by technology
Method used
Image
Examples
Embodiment Construction
[0016] The present invention will be further explained below in conjunction with specific embodiments.
[0017] refer to Figure 1-3 , a laser welding quality monitoring device, comprising two mutually parallel first operating table 7 and a second operating table 2, the first operating table 7 is provided with a first conveyor belt 4 for transporting parts to be welded, the first operating table 7 is provided with a welding device, and the parts to be welded are transferred to the lower end of the welding device through the first conveyor belt 4 for welding, and the upper end side of the second operating table 7 is provided with a second conveyor belt 1 for transporting unqualified parts for welding. The other side of the upper end of the platform 7 is provided with a third conveyor belt 11 for conveying welding qualified parts, and a carrying platform 10 is provided between the second conveyor belt 1 and the third conveyor belt 11, and the lower end of the carrying platform 1...
PUM
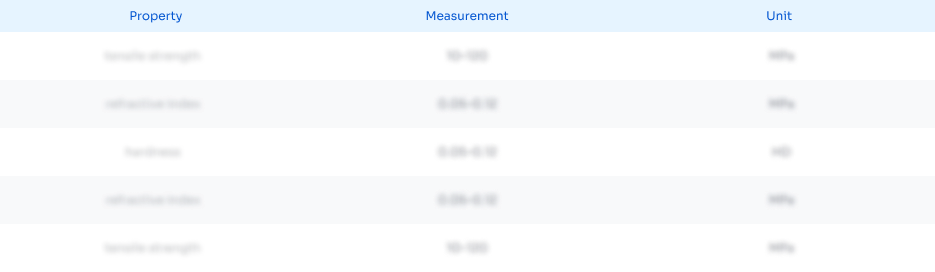
Abstract
Description
Claims
Application Information

- R&D
- Intellectual Property
- Life Sciences
- Materials
- Tech Scout
- Unparalleled Data Quality
- Higher Quality Content
- 60% Fewer Hallucinations
Browse by: Latest US Patents, China's latest patents, Technical Efficacy Thesaurus, Application Domain, Technology Topic, Popular Technical Reports.
© 2025 PatSnap. All rights reserved.Legal|Privacy policy|Modern Slavery Act Transparency Statement|Sitemap|About US| Contact US: help@patsnap.com