Butadiene-acrylonitrile toughened epoxy adhesive
A technology of tough epoxy and nitrile, which is applied in the field of preparation of nitrile toughened epoxy adhesive, can solve the problem of poor compatibility of epoxy resin and nitrile rubber modification, and the blending and modification phase of epoxy resin and nitrile rubber. Poor compatibility and other problems, to achieve the effect of solving poor compatibility
- Summary
- Abstract
- Description
- Claims
- Application Information
AI Technical Summary
Problems solved by technology
Method used
Examples
Embodiment 1
[0008] Accurately weigh 25 g of carboxyl-terminated liquid nitrile rubber with an acrylonitrile content of 25% and a functionality of 1.8, 100 g of solid epoxy resin E-20, 3 g of liquid epoxy resin E-51, and 7 g of 4-functional epoxy resin g and catalyst triethylamine 0.3g, put into the reaction kettle, heat up to 140°C, when the material in the kettle is completely in a liquid state, start stirring at a speed of 133rpm, fill with nitrogen protection after reacting for 1h, then react for 3h, and control the acid value Below 1.0, lower the temperature to 90°C, add 1.5g of silane coupling agent γ-aminopropyltriethoxysilane and 5g of curing agent dicyandiamide, stir for 40min and discharge to obtain solid glue.
Embodiment 2
[0010] Accurately weigh 20 g of carboxyl-terminated liquid nitrile rubber with an acrylonitrile content of 25% and a functionality of 1.8, 100 g of solid epoxy resin E-20, 3 g of liquid epoxy resin E-51, and 7 g of 4-functional epoxy resin g and catalyst triethylamine 0.3g, put into the reaction kettle, heat up to 140°C, when the material in the kettle is completely in a liquid state, start stirring at a speed of 133rpm, fill with nitrogen protection after reacting for 1h, then react for 3h, and control the acid value Below 1.0, lower the temperature to 80°C, add 1.5g of silane coupling agent γ-aminopropyltriethoxysilane and 5g of curing agent dicyandiamide, stir for 30min, and discharge to obtain a solid glue.
Embodiment 3
[0012] Accurately weigh 30 g of carboxyl-terminated liquid nitrile rubber with an acrylonitrile content of 25% and a functionality of 1.8, 100 g of solid epoxy resin E-20, 3 g of liquid epoxy resin E-51, and 7 g of 4-functional epoxy resin g and catalyst triethylamine 0.3g, put into the reaction kettle, heat up to 150°C, when the material in the kettle is completely in a liquid state, start stirring at a speed of 133rpm, fill with nitrogen protection after reacting for 1h, then react for 3h, and control the acid value Below 1.0, lower the temperature to 90°C, add 1.5g of silane coupling agent γ-aminopropyltriethoxysilane and 5g of curing agent dicyandiamide, stir for 50min and discharge to obtain solid glue.
PUM
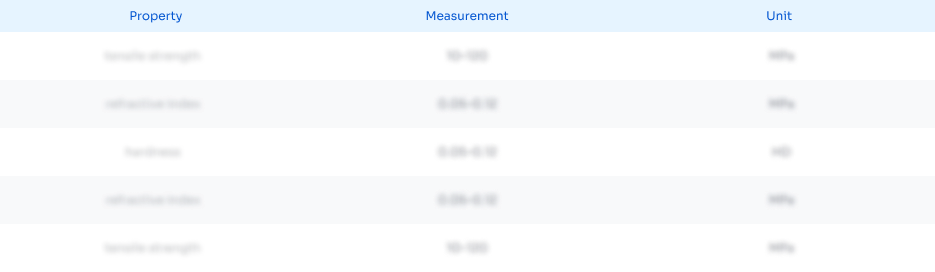
Abstract
Description
Claims
Application Information

- Generate Ideas
- Intellectual Property
- Life Sciences
- Materials
- Tech Scout
- Unparalleled Data Quality
- Higher Quality Content
- 60% Fewer Hallucinations
Browse by: Latest US Patents, China's latest patents, Technical Efficacy Thesaurus, Application Domain, Technology Topic, Popular Technical Reports.
© 2025 PatSnap. All rights reserved.Legal|Privacy policy|Modern Slavery Act Transparency Statement|Sitemap|About US| Contact US: help@patsnap.com