Production method for producing low-carbon low-silicon and aluminum-containing steel through short process
A low-carbon, low-silicon, production method technology, which is applied in the field of metallurgical processes, can solve the problems affecting the continuity of continuous casting production, high inclusion content, and high free oxygen content, so as to avoid the risk of excessive Si content, improve the compliance rate, and reduce The effect of returning to Si level
- Summary
- Abstract
- Description
- Claims
- Application Information
AI Technical Summary
Problems solved by technology
Method used
Examples
Embodiment 1
[0023] A production method of short-flow low-carbon, low-silicon and aluminum-containing steel, comprising the following steps, the first step, molten iron pretreatment: removing S in molten iron by KR molten iron deep desulfurization technology to a content weight percentage of S in molten iron ≤ 0.008 %, after treatment, the exposed area from slag removal to molten iron is ≥ 70%;
[0024] The second step, converter steelmaking: pour the molten iron obtained in step one into the converter steelmaking to ensure that the slag in the converter process is good. It is best to control to ensure that the composition of aluminum is qualified;
[0025] Step 3: Converter tapping operation: Pour the molten steel obtained in Step 2 into the ladle containing the molten steel. Double slag blocking is used for tapping in converter steelmaking, that is, the slag blocking cap is used at the beginning of tapping, and the sliding plate is used to block slag at the later stage of tapping to real...
Embodiment 2
[0037] A production method of short-flow low-carbon, low-silicon and aluminum-containing steel, comprising the following steps, the first step, hot metal pretreatment: removing S from hot metal by KR hot metal deep desulfurization technology to a content weight percentage of S in hot metal ≤ 0.005 %, after treatment, the exposed area from slag removal to molten iron is ≥ 70%;
[0038] The second step, converter steelmaking: pour the molten iron obtained in step one into the converter steelmaking to ensure that the slag in the converter process is good, and the temperature at the end point of the converter is controlled at 1682°C. Make appropriate adjustments according to the conditions of the ladle. The oxygen at the end point of the converter is 600ppm; It is best to control to ensure that the composition of aluminum is qualified;
[0039]Step 3: Converter tapping operation: Pour the molten steel obtained in Step 2 into the ladle containing the molten steel. Double slag block...
PUM
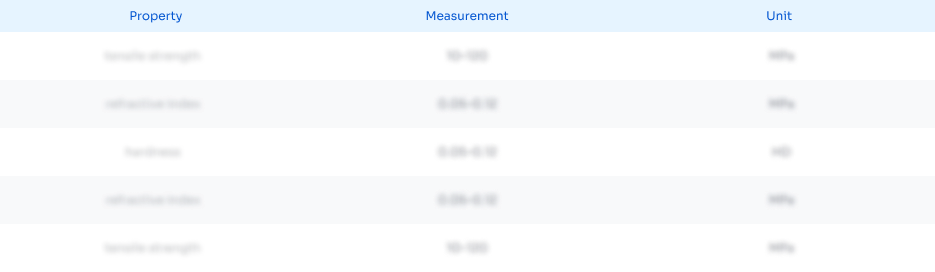
Abstract
Description
Claims
Application Information

- R&D
- Intellectual Property
- Life Sciences
- Materials
- Tech Scout
- Unparalleled Data Quality
- Higher Quality Content
- 60% Fewer Hallucinations
Browse by: Latest US Patents, China's latest patents, Technical Efficacy Thesaurus, Application Domain, Technology Topic, Popular Technical Reports.
© 2025 PatSnap. All rights reserved.Legal|Privacy policy|Modern Slavery Act Transparency Statement|Sitemap|About US| Contact US: help@patsnap.com