Method for manufacturing injection molding rod
A manufacturing method and technology of injection molding rods, which are applied in the direction of household components, household appliances, and other household appliances, can solve the problems of lack of cushioning plastics, easily damaged screw teeth, and increased weight, so as to avoid waste of raw materials, enhance aesthetics, and increase effect of weight
- Summary
- Abstract
- Description
- Claims
- Application Information
AI Technical Summary
Problems solved by technology
Method used
Image
Examples
Embodiment Construction
[0018] In order to make the object, technical solution and advantages of the present invention clearer, the present invention will be further described in detail below in conjunction with the accompanying drawings and specific embodiments. It should be understood that the specific embodiments described here are only used to explain the present invention, and are not intended to limit the present invention.
[0019] A method for making an injection molding rod, comprising the steps of:
[0020] Step 1: making a mould, which includes a mold for the covers at both ends of the injection rod and a mold for the rod of the injection rod. Feasibly, the molds for the covers at both ends are cylindrical grooves, and the injection-molded covers are in the shape of hollow cylinders. see figure 1 , is a schematic diagram of the mold structure of the injection rod in this specific embodiment, which includes two cavities. In other specific embodiments of the present invention, multiple cav...
PUM
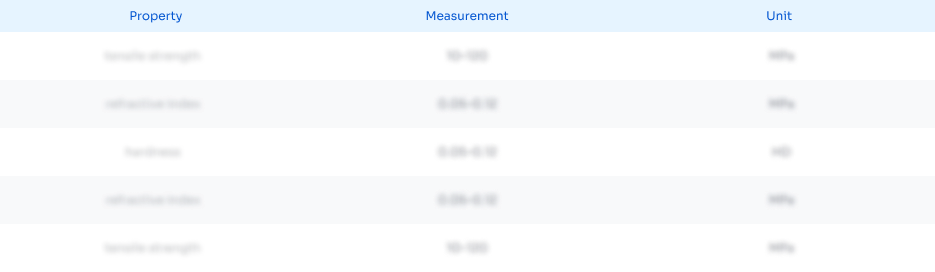
Abstract
Description
Claims
Application Information

- R&D Engineer
- R&D Manager
- IP Professional
- Industry Leading Data Capabilities
- Powerful AI technology
- Patent DNA Extraction
Browse by: Latest US Patents, China's latest patents, Technical Efficacy Thesaurus, Application Domain, Technology Topic, Popular Technical Reports.
© 2024 PatSnap. All rights reserved.Legal|Privacy policy|Modern Slavery Act Transparency Statement|Sitemap|About US| Contact US: help@patsnap.com