Corrosion-resisting austenitic stainless steel submerged-arc welding wire and production method thereof
A technology of austenitic stainless steel and production method, applied in welding medium, welding equipment, welding/cutting medium/material, etc., can solve the problems of insufficient tensile strength, insufficient mechanical properties of welds, high cost, and avoid intergranular Corrosion, simple process, effect of improving strength
- Summary
- Abstract
- Description
- Claims
- Application Information
AI Technical Summary
Problems solved by technology
Method used
Image
Examples
Embodiment
[0039] In this example, 3 batches of welding wires were trial-produced, and the welding wires of the comparative example were prepared through the same production process, all of which went through batching→vacuumizing→filling with argon→powering→full melting→cooling→adding ferrosilicon→adding carbon→adding titanium→ Power outage → pouring, steel ingot steelmaking process after cooling, and then forging, the initial forging temperature is 1230 ° C, the final forging temperature is 950 ° C, and rolling is carried out after air cooling. After multi-pass rolling, a semi-finished product with a diameter of 5.5 mm is obtained. The intermediate annealing temperature is 1150°C; after the annealing is completed, surface grinding treatment is carried out to treat surface cracks; the semi-finished product with a diameter of 5.5mm is drawn to 2.5mm, and solution heat treatment is performed at a temperature of 1150°C to obtain a finished welding wire. Its chemical composition is shown in T...
PUM
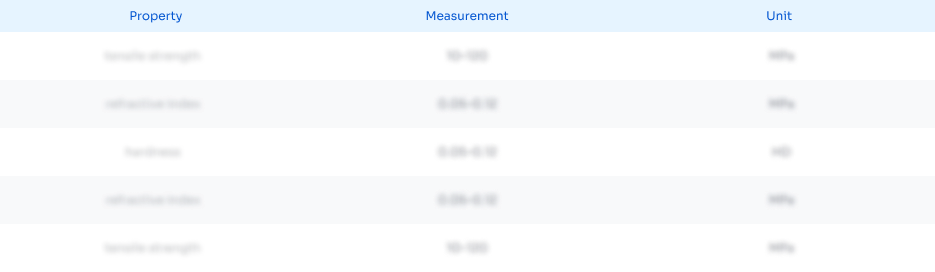
Abstract
Description
Claims
Application Information

- R&D
- Intellectual Property
- Life Sciences
- Materials
- Tech Scout
- Unparalleled Data Quality
- Higher Quality Content
- 60% Fewer Hallucinations
Browse by: Latest US Patents, China's latest patents, Technical Efficacy Thesaurus, Application Domain, Technology Topic, Popular Technical Reports.
© 2025 PatSnap. All rights reserved.Legal|Privacy policy|Modern Slavery Act Transparency Statement|Sitemap|About US| Contact US: help@patsnap.com