A kind of modification method and application of cation exchange resin catalyst
A cation exchange and catalyst technology, which is applied in the application of modified cation exchange resin catalysts and the field of modification of cation exchange resin catalysts, can solve the problems of low activity of modified resin catalysts, complex and cumbersome separation operations, and difficult disassembly of catalysts. Achieve the effect of low production cost, simple process and easy disassembly
- Summary
- Abstract
- Description
- Claims
- Application Information
AI Technical Summary
Problems solved by technology
Method used
Image
Examples
Embodiment 1
[0045] Embodiment 1 NKC-9 modified 1 # Preparation of:
[0046] Add 2.75 g of anhydrous aluminum trichloride and 200 ml of absolute ethanol into a 500 ml round bottom flask respectively, and stir to dissolve the anhydrous aluminum trichloride. Add 180 grams of NKC-9 resin and the ethanol solution dissolved with anhydrous aluminum trichloride into the reaction kettle respectively, install the reaction kettle (in a closed state to prevent the solvent from volatilizing), and heat it to 80°C under stirring. After 2 hours, cool down and stop stirring. After the temperature of the reactor is lowered to room temperature, the reactor is disassembled, the catalyst is poured out, dried in the air and baked at 80°C for 4 hours, and then taken out and placed in a desiccator for later use.
Embodiment 2
[0047] Embodiment 2 NKC-9 modified 2 # Preparation of:
[0048] Add 2.0 g of sulfamic acid and 200 ml of methanol into a 500 ml round bottom flask, stir to dissolve the sulfamic acid. Add 180 grams of NKC-9 resin and methanol solution dissolved with sulfamic acid into the reaction kettle respectively, install the reaction kettle (in a closed state to prevent the solvent from volatilizing), heat it to 80°C under stirring, and after 2 hours Cool down, stop stirring, disassemble the reactor after the temperature of the reactor drops to room temperature, pour out the catalyst, dry it in the air and bake it at 80°C for 4 hours, take it out and put it in a desiccator for later use.
Embodiment 3
[0049] Embodiment 3 NKC-9 modified 3 # Preparation of:
[0050] Add 2.75 grams of p-toluenesulfonic acid and 200 milliliters of methanol into a 500 milliliter round bottom flask, stir to dissolve the sulfamic acid. Add 200 grams of NKC-9 resin and methanol solution dissolved with p-toluenesulfonic acid into the reaction kettle respectively, install the reaction kettle (in a closed state to prevent the solvent from volatilizing), and stir at room temperature (25°C) 2 hours. Stop stirring and disassemble the reaction kettle, pour out the catalyst, dry it at 80°C for 4 hours, take it out and put it in a desiccator for later use.
PUM
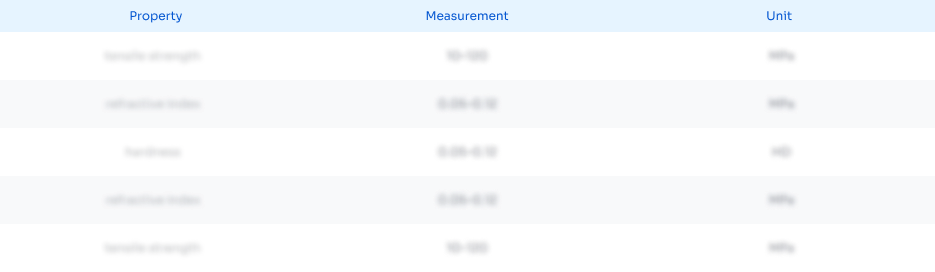
Abstract
Description
Claims
Application Information

- Generate Ideas
- Intellectual Property
- Life Sciences
- Materials
- Tech Scout
- Unparalleled Data Quality
- Higher Quality Content
- 60% Fewer Hallucinations
Browse by: Latest US Patents, China's latest patents, Technical Efficacy Thesaurus, Application Domain, Technology Topic, Popular Technical Reports.
© 2025 PatSnap. All rights reserved.Legal|Privacy policy|Modern Slavery Act Transparency Statement|Sitemap|About US| Contact US: help@patsnap.com