Preparation method for smelting high-silicon low-carbon silicomanganese alloy through one-step addition of silicon
A one-time, manganese alloy technology, which is applied in the field of ferroalloy preparation, can solve the problems of workers' difficulty in operating the furnace at high temperature, rising of the furnace's low slag surface, and cost increase.
- Summary
- Abstract
- Description
- Claims
- Application Information
AI Technical Summary
Problems solved by technology
Method used
Image
Examples
Embodiment 1
[0023] The preparation method of smelting high-silicon and low-carbon silicomanganese alloy with one-time external addition of silicon is to prepare a mixture with manganese content of 33.5%, silicon dioxide of 35%, and ferromanganese ratio of 5.0, and its particle size is 10mm-100mm; adding 25% of the mass of manganese ore coke, the carbon content of the coke is 80%, and its particle size is 25mm-40mm; add 6% of external silicon, the particle size is 10mm-100mm, and the content of phosphorus is 0.05%; the above-mentioned raw materials are continuously added to the submerged arc furnace, at 1600 Smelting above the temperature for 220 minutes, until the raw materials are completely melted, pour the liquid into the ladle, discharge the slag and iron out, and then cast it, you can directly get Mn ≥ 55%, Si ≥ 25%, P ≤ 0.1%, S ≤ 0.04%, C ≤ 0.3% high silicon low carbon silicon manganese alloy.
Embodiment 2
[0025] The preparation method of smelting high-silicon and low-carbon silicomanganese alloy with one-time external addition of silicon is to prepare a mixture with a mass content of 36.8% manganese, 38.5% silicon dioxide, and a ratio of manganese to iron of 8.8, with a particle size of 10mm-100mm; adding 26% manganese ore % of coke, the carbon content of coke is 80%, and its particle size is 25mm-40mm; add 7.5% of external silicon, the particle size is 10mm-100mm, and the content of phosphorus is 0.04%; the above raw materials are continuously added to the submerged arc furnace, and the Smelting above 1600 degrees for 220 minutes, until the raw materials are completely melted, pour the liquid into the ladder bag to discharge the slag and iron out, and then cast it, you can directly get Mn≥60%, Si≥27%, P≤0.1%, S≤0.02%, C≤0.2 % high silicon low carbon silicon manganese alloy.
Embodiment 3
[0027] The preparation method of smelting high-silicon and low-carbon silicomanganese alloy with one-time external addition of silicon is to prepare a mixture with a mass content of 37.5% manganese, 35% silicon dioxide, and a manganese-iron ratio of 9.2, and its particle size is 10mm-100mm; adding 26% manganese ore % of coke, the carbon content of coke is 80%, and its particle size is 25mm-40mm; add 7% of external silicon, the particle size is 10mm-100mm, and the total amount of phosphorus is 0.05%; The above smelting for 220 minutes, until the raw materials are completely melted, the liquid is poured into the ladder bag to discharge the slag and iron out, and then cast, and the Mn≥65%, Si≥25%, P≤0.12%, S≤0.03%, C≤0.3% can be directly obtained High silicon low carbon silicon manganese alloy.
PUM
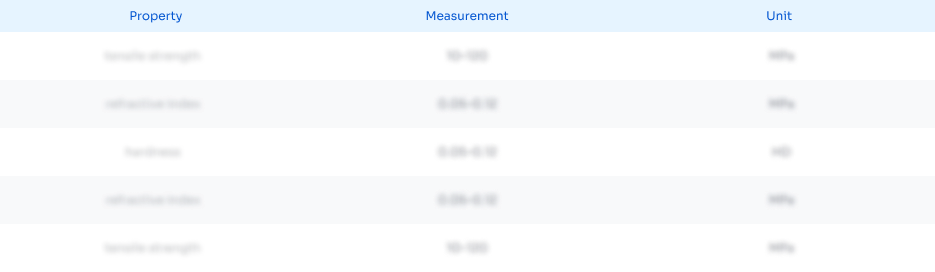
Abstract
Description
Claims
Application Information

- R&D Engineer
- R&D Manager
- IP Professional
- Industry Leading Data Capabilities
- Powerful AI technology
- Patent DNA Extraction
Browse by: Latest US Patents, China's latest patents, Technical Efficacy Thesaurus, Application Domain, Technology Topic, Popular Technical Reports.
© 2024 PatSnap. All rights reserved.Legal|Privacy policy|Modern Slavery Act Transparency Statement|Sitemap|About US| Contact US: help@patsnap.com