Reverse embossing machine
An embossing machine and rack technology, applied in the field of embossing, can solve the problems of ineffective utilization of thermal efficiency, achieve efficient utilization and improve preheating efficiency
- Summary
- Abstract
- Description
- Claims
- Application Information
AI Technical Summary
Problems solved by technology
Method used
Image
Examples
Embodiment Construction
[0017] Below, in conjunction with accompanying drawing and specific embodiment, the present invention is described further:
[0018] Such as Figure 1-3 As shown, the reverse side embossing machine includes a frame 10, a heating device 20, an embossing device 30 and a position adjustment device 40, and the heating device 20 includes a lampshade 21, a heat transfer oil ironing wheel 22 for preheating the non-embossed surface and a The heating lamp tube 23 on the heating embossing surface, the heat transfer oil ironing wheel 22 is rotatably connected to the frame 10; the heating lamp tube 23 is installed under the heat transfer oil ironing wheel 22, and the heating lamp tube 23 is covered in the lampshade 21; The lampshade 21 is fixed on the frame 10 in a detachable manner; the embossing device 30 includes an embossing wheel 31 for embossing patterns and a pressure wheel 32 for clamping; the embossing wheel 31 is rotatably connected to the frame 10; The wheel 32 is located abov...
PUM
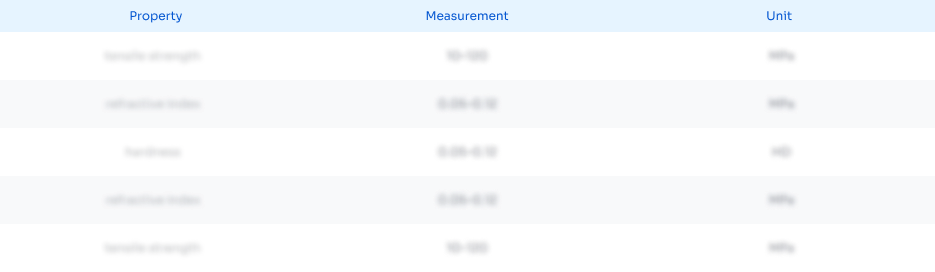
Abstract
Description
Claims
Application Information

- Generate Ideas
- Intellectual Property
- Life Sciences
- Materials
- Tech Scout
- Unparalleled Data Quality
- Higher Quality Content
- 60% Fewer Hallucinations
Browse by: Latest US Patents, China's latest patents, Technical Efficacy Thesaurus, Application Domain, Technology Topic, Popular Technical Reports.
© 2025 PatSnap. All rights reserved.Legal|Privacy policy|Modern Slavery Act Transparency Statement|Sitemap|About US| Contact US: help@patsnap.com