Method for recycling valuable elements in acidic biological oxidation solution containing arsenic, iron and sulfur
A technology of valuable element and oxidizing liquid, applied in the field of hydrometallurgy, can solve the problems of increasing production cost, waste of resources, consumption of large calcium oxide, etc., and achieve the effect of zero discharge of waste, low production cost and stable product quality
- Summary
- Abstract
- Description
- Claims
- Application Information
AI Technical Summary
Problems solved by technology
Method used
Image
Examples
Embodiment 1
[0027] (1) Add the oxidizing solution and extractant to the mixing clarifier, the extractant is 2-ethylhexyl phosphate mono-2-ethylhexyl, the volume ratio of the organic phase to the water phase is 1:0.5, stir at room temperature Mix for 3 minutes, then clarify for 15 minutes, through three-stage countercurrent extraction, the Fe in the oxidation solution 3+ The ions enter the organic phase, and the iron-loaded organic phase is back-extracted with a hydrochloric acid solution with a concentration of 3mol / L to recover the iron in the organic phase, and the organic phase is recycled. The recovery rate of iron is 95.06%;
[0028] (2) Add milk of lime to the raffinate, adjust the pH value of the solution to 7, stir for 10 hours at a temperature of 15°C, and a stirring intensity of 600r / min, and perform solid-liquid separation after completion, and the solid neutralized slag is acid leached The raw materials and valuable elements of the process all enter the neutralization slag, an...
Embodiment 2
[0034] (1) Add the oxidizing solution and extractant to the mixing clarifier, the extractant is 2-ethylhexyl phosphate mono-2-ethylhexyl, the volume ratio of the organic phase to the water phase is 1:1.0, stir at room temperature Mix for 5 minutes, then clarify for 15 minutes, after three-stage countercurrent extraction, the iron in the oxidizing solution enters the organic phase, and the iron-loaded organic phase is back-extracted with a hydrochloric acid solution with a concentration of 4mol / L, and the iron in the organic phase is recovered, and the organic phase is recycled. , the recovery rate of iron is 96.58%;
[0035] (2) Add milk of lime to the raffinate, adjust the pH of the solution to 8, stir at 20°C and 650r / min for 8 hours, and then separate the solid from the liquid, and the solid neutralized slag is acid leached The raw materials and valuable elements of the process all enter the neutralization slag, and through solid-liquid separation, the enrichment and separa...
Embodiment 3
[0041](1) Add the oxidizing solution and extractant to the mixing clarifier, the extractant is 2-ethylhexyl phosphate mono-2-ethylhexyl, the volume ratio of the organic phase to the water phase is 1:1.5, stir at room temperature Mix for 7 minutes, then clarify for 15 minutes, and through three-stage countercurrent extraction, the iron in the oxidizing solution enters the organic phase, and the iron-loaded organic phase is back-extracted with a hydrochloric acid solution with a concentration of 5mol / L, and the iron in the organic phase is recovered, and the organic phase is recycled. , the recovery rate of iron is 96.28%;
[0042] (2) Add milk of lime to the raffinate, adjust the pH of the solution to 8, stir for 6 hours at a temperature of 25°C, and a stirring intensity of 700r / min. After completion, carry out solid-liquid separation, and the solid neutralized slag is acid leached The raw materials and valuable elements of the process all enter the neutralization slag, and thr...
PUM
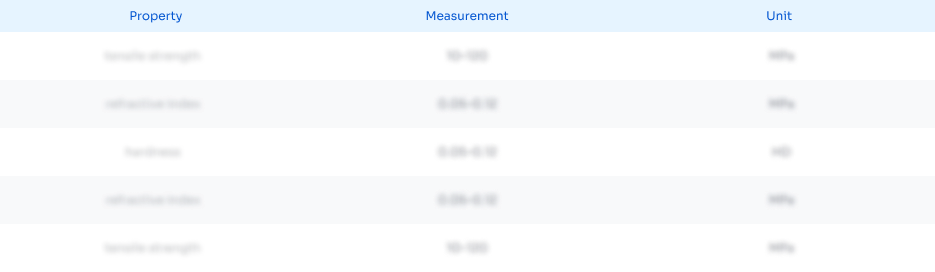
Abstract
Description
Claims
Application Information

- Generate Ideas
- Intellectual Property
- Life Sciences
- Materials
- Tech Scout
- Unparalleled Data Quality
- Higher Quality Content
- 60% Fewer Hallucinations
Browse by: Latest US Patents, China's latest patents, Technical Efficacy Thesaurus, Application Domain, Technology Topic, Popular Technical Reports.
© 2025 PatSnap. All rights reserved.Legal|Privacy policy|Modern Slavery Act Transparency Statement|Sitemap|About US| Contact US: help@patsnap.com