Nano zinc oxide modified epoxy resin composite material and preparation method thereof
A technology of nano-zinc oxide and epoxy resin, which is applied in the field of composite materials, can solve problems such as interface defects, material performance degradation, and weak bonding force of base materials, and achieve excellent nonlinear electrical properties, excellent partial discharge resistance, and improved resistance The effect of the electric level
- Summary
- Abstract
- Description
- Claims
- Application Information
AI Technical Summary
Problems solved by technology
Method used
Image
Examples
Embodiment 1
[0043] Step 1, weigh the following components by weight: 100 parts of bisphenol A epoxy resin E-51, 0.25 parts of KH570, 150 parts of water-acetone solution, 15 parts of nano zinc oxide, 100 parts of methyl tetrahydrophthalic anhydride, DMP-30 0.6 parts, DH410 10 parts;
[0044] Step 2, at room temperature, mix KH570 and water-acetone solution, adjust the pH to 6 with hydrochloric acid, and carry out the hydrolysis reaction for 3 hours; then add nano-zinc oxide, in a constant temperature water bath at 60°C, with a rotation speed of 1200r / min, stir for 60 minutes and then depressurize Filter, wash with deionized water until there is no chloride ion, and activate the product at 120°C for 9 hours after drying to obtain modified nano-zinc oxide;
[0045] Step 3, add the modified nano-zinc oxide obtained in step 2 into bisphenol A epoxy resin E-51, stir and sonicate at a speed of 1200r / min in a water bath at 50°C, and ultrasonically treat with a power of 200W , The frequency is 40...
Embodiment 2
[0050] Step 1, weigh the following components by weight: 100 parts of bisphenol A epoxy resin E-51, 0.35 parts of KH570, 100 parts of water-acetone solution, 10 parts of nano zinc oxide, 70 parts of methyl tetrahydrophthalic anhydride, 1 part of DMP-30, 12 parts of DH410;
[0051] Step 2, at room temperature, mix KH570 and water-acetone solution, adjust the pH to 5 with hydrochloric acid, and carry out the hydrolysis reaction for 3.5 hours; then add nano-zinc oxide, in a constant temperature water bath at 70°C, with a rotation speed of 1500r / min, stir for 50 minutes and then reduce Filter under pressure, wash with deionized water until there is no chloride ion, and activate the product at 140°C for 8 hours after drying to obtain modified nano-zinc oxide;
[0052] Step 3, add the modified nano-zinc oxide obtained in step 2 into bisphenol A epoxy resin E-51, stir and sonicate at a speed of 1500r / min in a water bath at 60°C, and ultrasonically treat with a power of 800W , Freque...
Embodiment 3
[0057] Step 1, weigh the following components by weight: 100 parts of bisphenol A epoxy resin E-51, 0.45 parts of KH570, 50 parts of water-acetone solution, 20 parts of nano-zinc oxide, 90 parts of methyltetrahydrophthalic anhydride, 2 copies of DMP-30, 8 copies of DH410;
[0058] Step 2, at room temperature, mix KH570 and water-acetone solution, adjust the pH to 4 with hydrochloric acid, and carry out the hydrolysis reaction for 4 hours; then add nano-zinc oxide, under a constant temperature water bath at 80°C, the speed is 1800r / min, stir for 40 minutes and then depressurize Filter, wash with deionized water until there is no chloride ion, and activate the product at 110°C for 9 hours after drying to obtain modified nano-zinc oxide;
[0059] Step 3, add the modified nano-zinc oxide obtained in step 2 into bisphenol A epoxy resin E-51, stir and sonicate at a speed of 1800r / min in a water bath at 70°C, and ultrasonically treat with a power of 400W , Frequency 20kHz, processin...
PUM
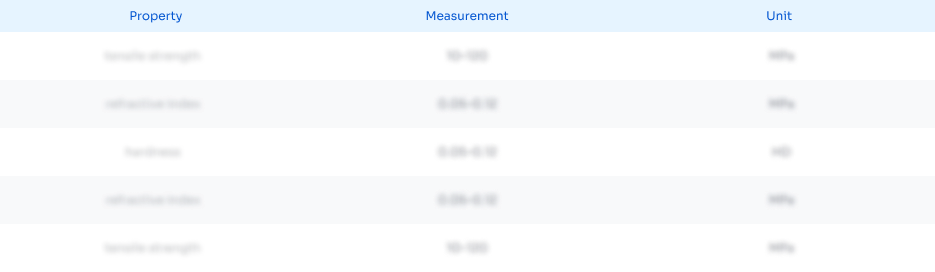
Abstract
Description
Claims
Application Information

- R&D Engineer
- R&D Manager
- IP Professional
- Industry Leading Data Capabilities
- Powerful AI technology
- Patent DNA Extraction
Browse by: Latest US Patents, China's latest patents, Technical Efficacy Thesaurus, Application Domain, Technology Topic.
© 2024 PatSnap. All rights reserved.Legal|Privacy policy|Modern Slavery Act Transparency Statement|Sitemap