Method for green-producing high-quality calcium superphosphate co-generated magnesium chloride by low-level collophanite
A green production and calcium superphosphate technology, applied in the direction of calcium superphosphate, magnesium chloride, chemical instruments and methods, etc., can solve problems such as impurity interference, achieve the effect of reducing magnesium content and increasing the content of phosphorus pentoxide in phosphate rock
- Summary
- Abstract
- Description
- Claims
- Application Information
AI Technical Summary
Problems solved by technology
Method used
Image
Examples
Embodiment 1
[0042] P in dry ore 2 o 5 , the contents of CaO and MgO are 22.74%, 40.64%, and 4.96%. With mechanical stirring, add phosphate rock slurry containing 210 grams of dry ore, take 105 mL of concentrated hydrochloric acid and add 105 mL of tap water, mix well and add to the constant pressure funnel, and react It is carried out at room temperature, and 1:1 hydrochloric acid is quickly added dropwise while the slurry is stirring. After the drop is completed, the reaction is continued for 15 minutes and then stopped, filtered with suction, and the solid is dried and weighed, and the weight is 155.4 grams. P in the solid phosphate concentrate 2 o 5 and MgO content are 29.04% and 1.32% respectively, which are directly used to prepare high-quality general calcium. Add 18mL of concentrated sulfuric acid equivalent to the amount of calcium ion substance in the obtained acid hydrolysis filtrate, and obtain calcium sulfate by centrifugal washing and drying, and remove calcium filtrate Ad...
Embodiment 2
[0044] P in dry ore 2 o 5 , the contents of CaO and MgO are 22.65%, 32.5%, and 7.8%. With mechanical stirring, add phosphate rock slurry containing 417.3 grams of dry ore, take 220mL of concentrated hydrochloric acid and add 220mL of tap water, mix well and add to the constant pressure funnel, and react It is carried out at room temperature, and 1:1 hydrochloric acid is quickly added dropwise while the slurry is stirring. After the drop is completed, the reaction is continued for 25 minutes, then stopped, filtered with suction, and the solid is dried and weighed, with a weight of 315.1 grams. P in the solid phosphate concentrate 2 o 5 , each content of MgO is 30.02%, 1.32%, add 37.5mL of concentrated sulfuric acid equivalent to the amount of calcium ion substance in the filtrate, get calcium sulfate through centrifugal washing, drying, add 90-100 milliliters of concentrated hydrochloric acid in the filtrate that removes calcium, be mixed with After 1:1 hydrochloric acid, ta...
PUM
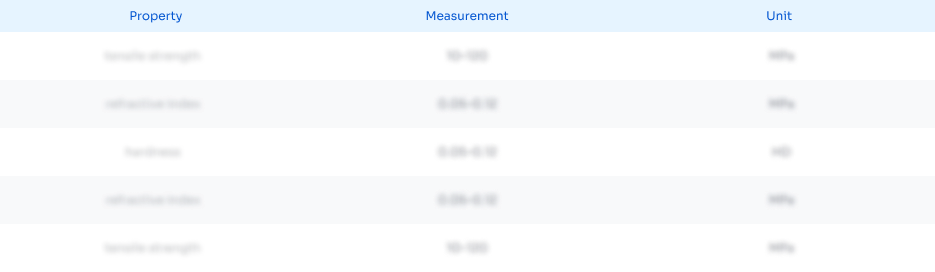
Abstract
Description
Claims
Application Information

- Generate Ideas
- Intellectual Property
- Life Sciences
- Materials
- Tech Scout
- Unparalleled Data Quality
- Higher Quality Content
- 60% Fewer Hallucinations
Browse by: Latest US Patents, China's latest patents, Technical Efficacy Thesaurus, Application Domain, Technology Topic, Popular Technical Reports.
© 2025 PatSnap. All rights reserved.Legal|Privacy policy|Modern Slavery Act Transparency Statement|Sitemap|About US| Contact US: help@patsnap.com