Smelting furnace heated through combination of heavy oil burning, gas burning and electric arc heating
A heavy oil combustion and gas combustion technology, applied in the field of heating smelting furnaces and smelting furnaces, can solve the problems of unstable combustion, control of the temperature in the furnace, and narrow applicability of raw materials, so as to speed up smelting and reduction, and achieve a reasonable and reasonable rate. The effect of controlling cost and avoiding oxidation phenomenon
- Summary
- Abstract
- Description
- Claims
- Application Information
AI Technical Summary
Problems solved by technology
Method used
Image
Examples
specific Embodiment approach 1
[0048] A heavy oil combustion, gas and electric arc combined heating smelting furnace, its structure is as follows figure 1 Shown: including furnace foundation 1, refractory material furnace bottom 2a, 2b, furnace body side wall 3 made of refractory bricks and refractory material with built-in cooling copper water jacket, partition wall 4 between the melting zone and the settlement zone, Furnace roof 5 located above the furnace, feed inlet 6 located above the furnace roof in the melting zone, slag outlet 7 and hot metal outlet 8 located below the settling zone, 4 sets of heat storage located on opposite walls of the melting zone Type burner burner 9, regenerator 10a, 10b inside regenerator 10, blower 11, flue gas pipeline 12, gas pipeline 13a, 13b, graphite electrode 14 placed on the furnace roof of the settling zone.
[0049] The melting furnace is divided into a melting zone 15 and a settling zone 16. The melting zone 15 is further divided into a melting zone 15a and a melti...
specific Embodiment approach 2
[0054] A heavy oil combustion, gas and electric arc combined heating smelting furnace, its structure is as follows figure 1 Shown: including furnace foundation 1, refractory material furnace bottom 2a, 2b, furnace body side wall 3 made of refractory bricks and refractory material with built-in cooling copper water jacket, partition wall between melting zone 15 and settlement zone 16 4. Furnace roof 5 above the furnace, feed inlet 6 above the furnace roof in melting zone 15, slag outlet 7 and hot metal outlet 8 below settling zone 16, located on opposite walls of melting zone 15 3 sets of regenerative burner burners 9, regenerators 10a, 10b inside the regenerator 10, blower 11, flue gas pipeline 12, gas pipelines 13a, 13b, and graphite electrodes 14 placed on the roof of the settling zone.
[0055] The melting furnace can be divided into a melting zone 15 and a settling zone 16. The melting zone 15 is further divided into a melting zone 15a and a melting zone 15b. The melting z...
specific Embodiment approach 3
[0060] A heavy oil combustion, gas and electric arc combined heating smelting furnace, its structure is as follows figure 1 Shown: including furnace foundation 1, refractory material furnace bottom 2a, 2b, furnace body side wall 3 made of refractory bricks and refractory material with built-in cooling copper water jacket, partition wall between melting zone 15 and settlement zone 16 4. Furnace roof 5 above the furnace, feed inlet 6 above the furnace roof in melting zone 15, slag outlet 7 and hot metal outlet 8 below settling zone 16, located on opposite walls of melting zone 15 10 sets of regenerative burner burners 9, regenerators 10a, 10b inside the regenerator 10, blower 11, flue gas pipeline 12, gas pipelines 13a, 13b, graphite electrodes 14 placed on the roof of the settling zone.
[0061] The melting furnace can be divided into a melting zone 15 and a settling zone 16. The melting zone 15 is further divided into a melting zone 15a and a melting zone 15b. The melting zone...
PUM
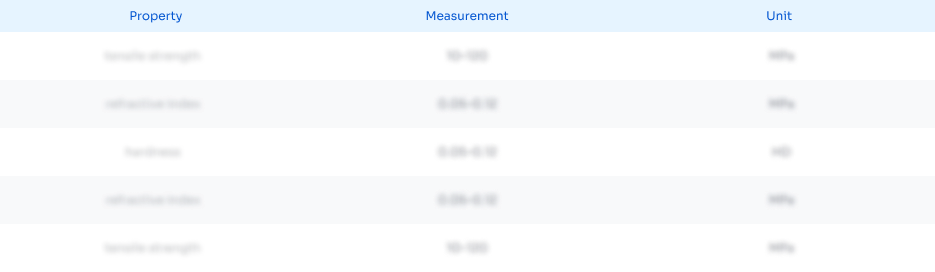
Abstract
Description
Claims
Application Information

- Generate Ideas
- Intellectual Property
- Life Sciences
- Materials
- Tech Scout
- Unparalleled Data Quality
- Higher Quality Content
- 60% Fewer Hallucinations
Browse by: Latest US Patents, China's latest patents, Technical Efficacy Thesaurus, Application Domain, Technology Topic, Popular Technical Reports.
© 2025 PatSnap. All rights reserved.Legal|Privacy policy|Modern Slavery Act Transparency Statement|Sitemap|About US| Contact US: help@patsnap.com