wood-plastic composite material for 3D (three-dimensional) printing
A wood-plastic composite material and 3D printing technology, applied in the field of wood-plastic composite materials for 3D printing, can solve the problems of composite material affinity and thermal deformation temperature modification, and achieve good toughness, broad market prospects and low price. Effect
- Summary
- Abstract
- Description
- Claims
- Application Information
AI Technical Summary
Problems solved by technology
Method used
Image
Examples
preparation example Construction
[0073] The preparation method of described wood-plastic composite material for 3D printing comprises the following steps:
[0074] S1: Pulverize the selected plant fiber and pass it through a 80-120 mesh sieve to obtain a powder. The powder is dried at 88-95°C for 2-2.8 hours, and the moisture content is controlled below 0.05% to obtain the primary raw material plant fiber powder ;
[0075] S2: Add polyolefin plastic powder, polylactic acid, potassium tripolyphosphate, ethylene glycol ether acetate, and specific synthetic agents to the primary raw material plant fiber powder prepared in step S1, heat up to 175-206°C, and rotate at 200°C Stir and melt at -400r / min for 1.5-3.5h, then cool to room temperature to obtain a modified plant fiber 3D printing secondary material;
[0076] The preparation method of described specific synthetic agent, comprises the following steps:
[0077] S21: Mix the generator, coupling agent a, compatibilizer, and antioxidant and heat up to 119-126°...
Embodiment 1
[0088] A wood-plastic composite material for 3D printing, in parts by weight, comprising the following raw materials: 120 parts of plant fiber powder, 135 parts of polyolefin plastic powder, 45 parts of polylactic acid, 28 parts of potassium tripolyphosphate, ethylene glycol ether acetic acid 27 parts of ester, 20 parts of specific synthetic agent, 12 parts of starch synthetic agent;
[0089] The specific synthetic agent is in parts by weight, including the following raw materials: 18 parts of regulator, 15 parts of generating agent, 12 parts of coupling agent a, 15 parts of compatibilizer, 10 parts of plasticizer, 12 parts of antioxidant, coagulation 8 parts of agent, 4 parts of terminator;
[0090] The plant fiber is eucalyptus fiber;
[0091] The regulator is ACR;
[0092] The generating agent is an aerosol generating agent;
[0093] The coupling agent a is water-soluble silane;
[0094] The compatibilizer is an acrylic acid type compatibilizer;
[0095] Described plas...
Embodiment 2
[0124] A wood-plastic composite material for 3D printing, in parts by weight, comprising the following raw materials: 96 parts of plant fiber powder, 114 parts of polyolefin plastic powder, 38 parts of polylactic acid, 24 parts of potassium tripolyphosphate, ethylene glycol ether acetic acid 26 parts of ester, 16 parts of specific synthetic agent, 8 parts of starch synthetic agent;
[0125] The specific synthetic agent is in parts by weight, including the following raw materials: 14 parts of regulator, 12 parts of generating agent, 10 parts of coupling agent a, 14 parts of compatibilizer, 9 parts of plasticizer, 7 parts of antioxidant, coagulation 6 parts of agent, 3 parts of terminator;
[0126] The plant fiber is eucalyptus fiber;
[0127] The regulator is ACR;
[0128] The generating agent is an aerosol generating agent;
[0129] The coupling agent a is water-soluble silane;
[0130] The compatibilizer is an acrylic acid type compatibilizer;
[0131] Described plastici...
PUM
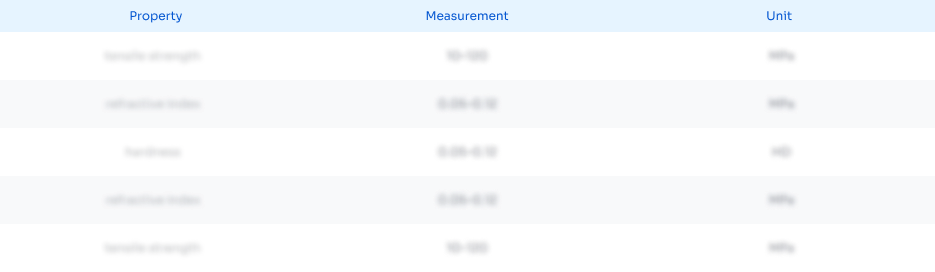
Abstract
Description
Claims
Application Information

- R&D Engineer
- R&D Manager
- IP Professional
- Industry Leading Data Capabilities
- Powerful AI technology
- Patent DNA Extraction
Browse by: Latest US Patents, China's latest patents, Technical Efficacy Thesaurus, Application Domain, Technology Topic, Popular Technical Reports.
© 2024 PatSnap. All rights reserved.Legal|Privacy policy|Modern Slavery Act Transparency Statement|Sitemap|About US| Contact US: help@patsnap.com