Powder-bed additive manufacturing devices and methods
A powder bed and metal powder technology, applied in the field of powder bed additive manufacturing equipment, can solve the problem of not maintaining the thermal profile of the added layer
- Summary
- Abstract
- Description
- Claims
- Application Information
AI Technical Summary
Problems solved by technology
Method used
Image
Examples
Embodiment Construction
[0065] Reference will now be made in detail to exemplary embodiments of the present disclosure, examples of which are illustrated in the accompanying drawings. Wherever possible, the same reference numbers will be used throughout the drawings to refer to the same or like parts.
[0066] figure 1 An exemplary powder bed fusion additive manufacturing apparatus 10 for manufacturing or forming at least one metal alloy component free of cracks in accordance with the present disclosure is shown. In one example, the component is a crack-free high temperature superalloy component. The terms crack free and the like are used herein to mean that the layers of metal alloy components or component parts formed by the powder bed fusion apparatus 10 are free from thermally induced cracks in their microstructure after solidification. In one example, apparatus 10 is capable of forming metal alloy components (or portions thereof) via layers without thermally induced cracks approximately 100 mi...
PUM
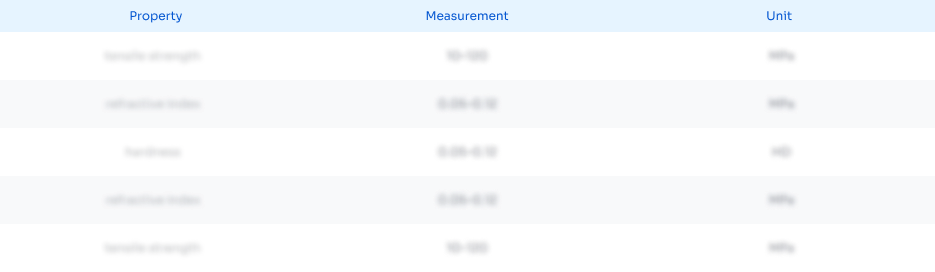
Abstract
Description
Claims
Application Information

- Generate Ideas
- Intellectual Property
- Life Sciences
- Materials
- Tech Scout
- Unparalleled Data Quality
- Higher Quality Content
- 60% Fewer Hallucinations
Browse by: Latest US Patents, China's latest patents, Technical Efficacy Thesaurus, Application Domain, Technology Topic, Popular Technical Reports.
© 2025 PatSnap. All rights reserved.Legal|Privacy policy|Modern Slavery Act Transparency Statement|Sitemap|About US| Contact US: help@patsnap.com