Method for reducing enzyme usage amount in process of producing acrylamide by virtue of microbiological method
A technology for using acrylamide nitrile hydratase and microbial method, which is applied in the field of reducing the amount of enzyme used in the process of producing acrylamide by microbial method, and can solve the problem of lowering the quality of acrylamide products, reducing the activity of nitrile hydratase, and increasing the amount of fermentation broth used. question
- Summary
- Abstract
- Description
- Claims
- Application Information
AI Technical Summary
Problems solved by technology
Method used
Examples
Embodiment 1
[0007] a. At 8m 3 The nitrile hydratase fermented broth ultrafiltration circulating tank was added with 4 m of fermented broth with storage time ≥ 240 hours 3 , after being ultrafiltered by an ultrafiltration membrane, put it into an ultrafiltrate storage tank, and store it at 4±1°C as a backup biocatalyst for catalytic hydration.
[0008] b. At 25m 3 In the catalytic reactor, add 17 m 3 of water, add 1.2m 3 For the nitrile hydratase fermentation broth, start to feed acrylonitrile into the catalytic reaction kettle from the high-position metering tank.
[0009] c. Control the catalytic reaction temperature between 20°C and 28°C, and control the content of acrylonitrile to <0.1% (check once every half hour).
[0010] d. Final reaction solution: acrylamide content 32%~34%, acrylonitrile content ≤0.005%, as the reaction end point.
[0011] e. Product quality indicators are shown in Table 1 below.
Embodiment 2
[0013] a. At 8m 3 The nitrile hydratase fermented liquid ultrafiltration circulating tank adds the fermented liquid 4 m of storage time 50 hours 3 , after being ultrafiltered by an ultrafiltration membrane, put it into an ultrafiltrate storage tank, and store it at 4±1°C as a backup biocatalyst for catalytic hydration.
[0014] b. At 25m 3 In the catalytic reactor, add 17 m 3 water, add 0.3m 3 For the nitrile hydratase fermentation broth, start to feed acrylonitrile into the catalytic reaction kettle from the high-position metering tank.
[0015] c. Control the catalytic reaction temperature between 20°C and 28°C, and control the content of acrylonitrile to <0.1% (check once every half hour).
[0016] d. Final reaction solution: acrylamide content 32%~34%, acrylonitrile content ≤0.005%, as the reaction end point.
[0017] e. Product quality indicators are shown in Table 1 below.
Embodiment 3
[0019] a. At 8m 3 The nitrile hydratase fermented liquid ultrafiltration circulating tank adds the fermented liquid 4 m of storage time 120 hours 3 , after being ultrafiltered by an ultrafiltration membrane, put it into an ultrafiltrate storage tank, and store it at 4±1°C as a backup biocatalyst for catalytic hydration.
[0020] b. At 25m 3 In the catalytic reactor, add 17 m 3 water, add 0.5m 3 For the nitrile hydratase fermentation broth, start to feed acrylonitrile into the catalytic reaction kettle from the high-position metering tank.
[0021] c. Control the catalytic reaction temperature between 20°C and 28°C, and control the content of acrylonitrile to <0.1% (check once every half hour).
[0022] d. Final reaction solution: acrylamide content 32%~34%, acrylonitrile content ≤0.005%, as the reaction end point.
[0023] e. Product quality indicators are shown in Table 1 below.
PUM
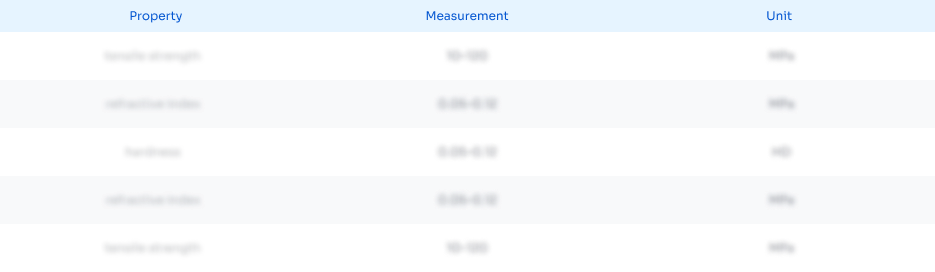
Abstract
Description
Claims
Application Information

- Generate Ideas
- Intellectual Property
- Life Sciences
- Materials
- Tech Scout
- Unparalleled Data Quality
- Higher Quality Content
- 60% Fewer Hallucinations
Browse by: Latest US Patents, China's latest patents, Technical Efficacy Thesaurus, Application Domain, Technology Topic, Popular Technical Reports.
© 2025 PatSnap. All rights reserved.Legal|Privacy policy|Modern Slavery Act Transparency Statement|Sitemap|About US| Contact US: help@patsnap.com