Novel muffle furnace
A muffle furnace, a new type of technology, applied in glass forming, glass blowing, glass manufacturing equipment, etc., can solve the problems of unguaranteed diameter and roundness of glass tubes, non-environmental waste gas, uneven temperature, etc., to achieve Uniform and controllable temperature, clean energy and environmental protection, high thermal efficiency
- Summary
- Abstract
- Description
- Claims
- Application Information
AI Technical Summary
Problems solved by technology
Method used
Image
Examples
Embodiment Construction
[0009] as attached figure 1 , 2 As shown, the heat-resistant plate 4 is made into a straight cylinder to form the furnace chamber 3 , and the outer periphery of the straight-cylindrical heating chamber 5 is made of a steel plate 6 to form the heating chamber 5 between the heat-resistant plate 4 and the steel plate 6 . Three silicon-molybdenum rods 2 are arranged on the radial section of each one-third of the axial direction from the heating chamber 5 and are separated in an equilateral triangle. Turn on the power supply of the silicon molybdenum rod 2 , the temperature in the heating chamber 5 is raised, and the temperature is transferred to the furnace chamber 3 through the heat-resistant plate 4 . When the temperature in the furnace cavity 3 rises to the set temperature, the silicon-molybdenum rod 2 is instructed by the temperature controller to be de-energized (to be energized after falling to the set temperature). Thus, the molten glass passes through the furnace chamber...
PUM
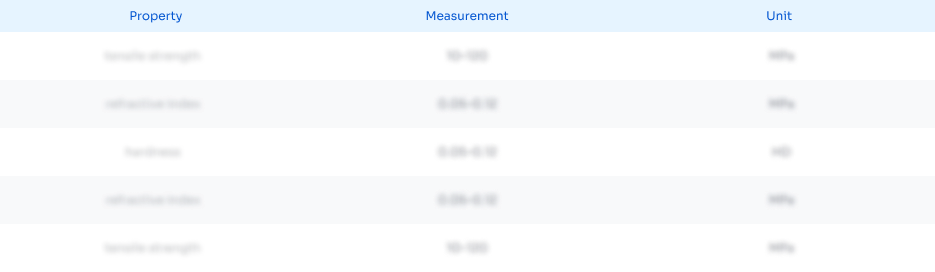
Abstract
Description
Claims
Application Information

- Generate Ideas
- Intellectual Property
- Life Sciences
- Materials
- Tech Scout
- Unparalleled Data Quality
- Higher Quality Content
- 60% Fewer Hallucinations
Browse by: Latest US Patents, China's latest patents, Technical Efficacy Thesaurus, Application Domain, Technology Topic, Popular Technical Reports.
© 2025 PatSnap. All rights reserved.Legal|Privacy policy|Modern Slavery Act Transparency Statement|Sitemap|About US| Contact US: help@patsnap.com