Electrode structure of electrolyte thermobattery and electrolyte thermobattery preparation method
A thermoelectric battery and electrode structure technology, applied in the manufacture/processing of thermoelectric devices, thermoelectric device components, thermoelectric devices using only Peltier or Seebeck effect, etc., can solve problems such as low thermoelectric efficiency, reduce heat loss and save energy Electrode material, cost reduction effect
- Summary
- Abstract
- Description
- Claims
- Application Information
AI Technical Summary
Problems solved by technology
Method used
Image
Examples
preparation example Construction
[0048] A method for preparing an electrolyte thermoelectric battery, comprising the following steps:
[0049] Step 1, designing the size, density and position of the column array electrode or sheet array electrode;
[0050] Use 3dmax or Autocad software to design and draw battery hot-end electrodes and battery cold-end electrodes with column arrays or sheet arrays, including determining the size of battery hot-end electrodes and battery cold-end electrodes, as well as the configuration of column array electrodes or sheet array electrodes Single quantity and position; design and draw the shape specification and size of insulating partition 3 at the same time;
[0051] Step 2: Use 3D printing technology to print out the battery hot terminal electrode, the battery cold terminal electrode and the insulating separator 3 respectively;
[0052] Use 3D printing technology to directly print the model diagram drawn above, wherein the raw materials used for the battery hot end electrode...
Embodiment 1
[0056] Example 1: Autocad software is used to design and draw electrodes with a column array, wherein the diameter of a single column array electrode is 0.5 mm, the length is 2 mm, and the distance between two adjacent column array electrodes is 1 mm. 3D printing technology is used to print the hot end, cold end electrodes, and insulating partitions respectively; the raw materials used for the hot end and cold end electrodes are titanium alloy powder; the material of the insulating partitions is ABS resin. After the hot-end and cold-end electrodes are printed, a 100-nm platinum layer is further vapor-deposited on the surface of the pillar array as an electrocatalytic active material. Put the hot-end electrode on the bottom, and then place the insulating partition on it to ensure that the column array part of the hot-end electrode completely enters the electrolyte groove part of the insulating partition; after sealing the hot-end electrode and the insulating partition, The elec...
Embodiment 2
[0057] Embodiment 2: adopt Autocad software to design and draw the electrode with slice array, wherein the length, width and height of each slice array electrode are 4 centimeters, 1 millimeter, and 2 centimeters respectively, and the distance between two adjacent array electrodes is 1 mm. 3D printing technology is used to print out the hot-end, cold-end electrodes, and insulating partitions respectively; the raw materials used for the hot-end and cold-end electrodes are stainless steel powder; the material of the insulating partitions is polycarbonate resin. After the hot-end and cold-end electrodes are printed, a 50-nm platinum layer is further vapor-deposited on the surface of the chip array as an electrocatalytic active material. Put the hot-end electrode on the bottom, and then place the insulating partition on it to ensure that the plate array part of the hot-end electrode completely enters the electrolyte groove part of the insulating partition; after sealing the hot-en...
PUM
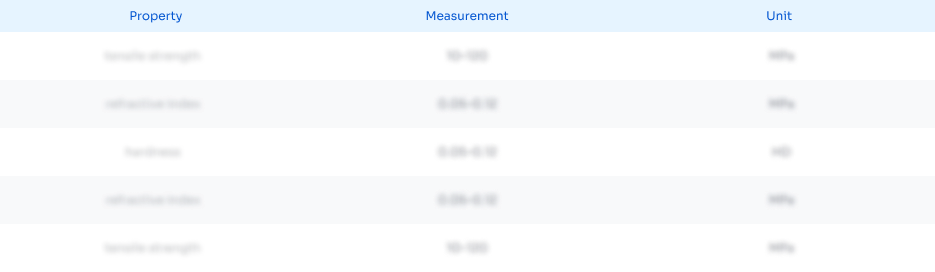
Abstract
Description
Claims
Application Information

- Generate Ideas
- Intellectual Property
- Life Sciences
- Materials
- Tech Scout
- Unparalleled Data Quality
- Higher Quality Content
- 60% Fewer Hallucinations
Browse by: Latest US Patents, China's latest patents, Technical Efficacy Thesaurus, Application Domain, Technology Topic, Popular Technical Reports.
© 2025 PatSnap. All rights reserved.Legal|Privacy policy|Modern Slavery Act Transparency Statement|Sitemap|About US| Contact US: help@patsnap.com