Production technology of yarn-dyed warp-wise tubular fabric
- Summary
- Abstract
- Description
- Claims
- Application Information
AI Technical Summary
Problems solved by technology
Method used
Image
Examples
specific Embodiment
[0056] The process steps of the present invention are as follows: loose winding → bobbin dyeing → rewinding → batch warping → sizing → piercing warp → weaving process → finishing.
[0057] 1. Loose winding
[0058] The winding machine is a common winding machine GA015; bobbins are fed. The commonly used winding range of GA015 winding machine is 500-900m / min, and the winding speed selected for this fabric is 600m / min. The weight of the tension washer is 7.4g, and it is wound into a loose tube to facilitate the penetration of the dye; in order to improve the quality of the fabric, the joints are jointed with a hand-held air splicer.
[0060] Warp yarn 40S cotton yarn, two colors of snow blue and white, dyed with reactive dyes. Dyeing prescription and conditions:
[0061] 40 S Snow green yarn dyeing process: reactive yellow BES 0.62%; reactive red BES 1.35%; reactive blue BET 2.52%; Yuanming powder 40g / L; soda ash 20g / L; liquor ratio 1:10; temperat...
PUM
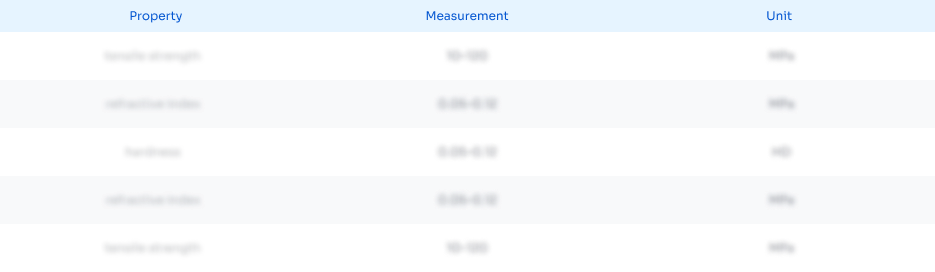
Abstract
Description
Claims
Application Information

- R&D Engineer
- R&D Manager
- IP Professional
- Industry Leading Data Capabilities
- Powerful AI technology
- Patent DNA Extraction
Browse by: Latest US Patents, China's latest patents, Technical Efficacy Thesaurus, Application Domain, Technology Topic, Popular Technical Reports.
© 2024 PatSnap. All rights reserved.Legal|Privacy policy|Modern Slavery Act Transparency Statement|Sitemap|About US| Contact US: help@patsnap.com