Double-coated paraffin microcapsule phase change material and preparation method thereof
A technology of paraffin microcapsules and phase change materials, applied in heat exchange materials, chemical instruments and methods, etc., can solve problems such as single wall material, and achieve the effects of prolonging service life, improving strength and excellent weather resistance.
- Summary
- Abstract
- Description
- Claims
- Application Information
AI Technical Summary
Problems solved by technology
Method used
Image
Examples
Embodiment 1
[0023] Step 1: Add 10 parts of No. 58 fully refined paraffin into the stirred tank, raise the temperature to 65°C; add 0.2 part of cetyltrimethylammonium bromide, 0.5 part of Span-60 and 0.5 part of Tween-60 , mixed evenly, and then slowly added 80 parts of deionized water; stirred at a stirring speed of 1500 r / min for 0.5 h to obtain an O / W type paraffin wax emulsion.
[0024] Step 2: Take 20 parts of the paraffin wax emulsion prepared in step 1, add 0.02 part of ammonium persulfate and 0.2 part of 0.5% lithium magnesium silicate solution, raise the temperature to 70°C, stir until the two dissolve, and then slowly add acrylic acid dropwise 5 parts of butyl ester and 2 parts of methyl methacrylate were dripped within 1 h, and then the reaction was incubated for 1 h.
[0025] Step 3: After the completion of step 2, add 0.02 part of ammonium persulfate, then slowly dropwise add 5 parts of methyl methacrylate, 2 parts of butyl acrylate and 1 part of acrylic acid, the dripping is ...
Embodiment 2
[0028] Step 1: Add 15 parts of RUBITHERM (34°C) to the stirring tank, raise the temperature to 70°C; add 0.5 part of dodecyl ammonium chloride, 0.5 part of Span-60 and 0.5 part of OP-10, mix well, Then slowly add 120 parts of deionized water; stir at a stirring speed of 1500r / min for 0.5h to obtain an O / W type paraffin wax emulsion.
[0029] Step 2: Take 30 parts of the paraffin wax emulsion prepared in step 1, add 0.04 part of ammonium sulfate and 0.4 part of 0.5% lithium magnesium silicate solution, raise the temperature to 70°C, stir until the two dissolve and start to slowly dropwise add isoacrylic acid. 8 parts of octyl ester and 3 parts of methyl methacrylate were dripped within 1 hour, and then the reaction was incubated for 1 hour.
[0030] Step 3: After the completion of step 2, add 0.04 part of ammonium persulfate, then slowly dropwise add 6 parts of epoxy acrylate, 2 parts of isooctyl acrylate and 2 parts of acrylic acid, the dripping is completed within 1 hour, and...
Embodiment 3
[0033] Step 1: Add 20 parts of RUBITHERM (44°C) to the stirred tank, raise the temperature to 70°C; add 1 part of cetylpyridinium bromide, 1 part of Span-80 and 1 part of OP-10, mix well, Then slowly add 160 parts of deionized water; stir at 3000r / min stirring speed for 0.5h to obtain O / W type paraffin wax emulsion.
[0034] Step 2: Take 45 parts of the paraffin wax emulsion prepared in step 1, add 0.05 part of potassium persulfate, 0.3 part of ethylene glycol and 0.2 part of propylene glycol, raise the temperature to 70°C, stir until the two dissolve, and then slowly add acrylic acid dropwise 10 parts of isooctyl ester and 3 parts of methyl methacrylate were dripped within 1 h, and then the reaction was incubated for 1 h.
[0035] Step 3: After the completion of step 2, 0.05 part of potassium persulfate was added, and then 10 parts of epoxy acrylate, 3 parts of isooctyl acrylate, 2 parts of acrylic acid and 1 part of hydroxyethyl acrylate were slowly added dropwise. The temp...
PUM
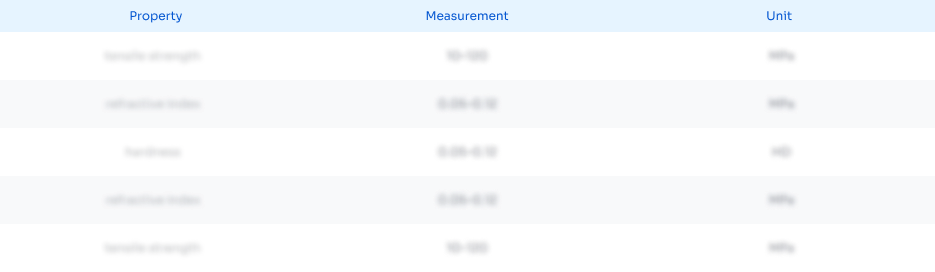
Abstract
Description
Claims
Application Information

- R&D
- Intellectual Property
- Life Sciences
- Materials
- Tech Scout
- Unparalleled Data Quality
- Higher Quality Content
- 60% Fewer Hallucinations
Browse by: Latest US Patents, China's latest patents, Technical Efficacy Thesaurus, Application Domain, Technology Topic, Popular Technical Reports.
© 2025 PatSnap. All rights reserved.Legal|Privacy policy|Modern Slavery Act Transparency Statement|Sitemap|About US| Contact US: help@patsnap.com