Main load-bearing structure suitable for ballistic reentry recovery capsule
A recovery cabin and main load-bearing technology, applied in space navigation equipment, space navigation vehicles, space navigation equipment, etc., can solve the problems of increasing the cost of testing and material processing, increasing the difficulty of design, increasing the weight of the structure, etc. , to achieve the effect of avoiding large loads, reducing component stress, and reducing stress concentration
- Summary
- Abstract
- Description
- Claims
- Application Information
AI Technical Summary
Problems solved by technology
Method used
Image
Examples
Embodiment Construction
[0039] The present invention will be described in detail below with reference to the accompanying drawings and examples.
[0040] The invention provides a main load-bearing structure suitable for a ballistic reentry recovery cabin, see attached Figure 1-6 , including: head shell 1, stabilizing skirt 2, skirt bottom 3, instrument panel 4, transition bracket 5, support seat 6, platform 7, umbrella cabin device 8, pull rod 9 and adjusting gasket 10;
[0041] The head shell 1 is a shell composed of a truncated cone and a spherical segment, wherein the bottom surface of the spherical segment is docked with the small end of the truncated cone;
[0042] The stable skirt 2 is a frustum-shaped shell, and three annular bosses coaxial with the stable skirt 2 are processed on the inner peripheral surface of the stable skirt 2 along its axial direction, which are respectively the upper end frame and the middle spacer frame of the stable skirt 2. And the bottom end frame; The upper end fr...
PUM
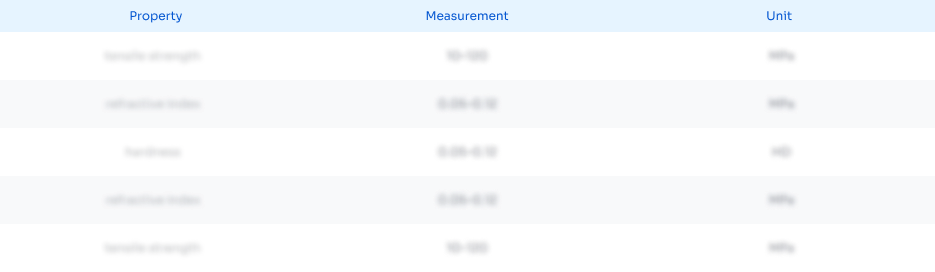
Abstract
Description
Claims
Application Information

- R&D Engineer
- R&D Manager
- IP Professional
- Industry Leading Data Capabilities
- Powerful AI technology
- Patent DNA Extraction
Browse by: Latest US Patents, China's latest patents, Technical Efficacy Thesaurus, Application Domain, Technology Topic, Popular Technical Reports.
© 2024 PatSnap. All rights reserved.Legal|Privacy policy|Modern Slavery Act Transparency Statement|Sitemap|About US| Contact US: help@patsnap.com