Forging method of Cr18Mn18N steel forge piece and forge piece
A cr18mn18n, C-1210 technology, applied in the direction of metal processing equipment, etc., can solve the problems of deformed crystals, serious surface cracks, coarse crystals and mixed crystals, etc., and achieve the effects of small microscopic defects, complete metal streamlines and good processing performance
- Summary
- Abstract
- Description
- Claims
- Application Information
AI Technical Summary
Problems solved by technology
Method used
Examples
Embodiment 1
[0029] The forging method of the Cr18Mn18N steel forging provided by the present embodiment comprises the following steps:
[0030] Forging blanking:
[0031] The billet made of Cr18Mn18N steel is heated to the steel ingot heating temperature of 1220°C-1240°C and released from the furnace, and upsetting is performed to the height H of the whole ingot of 1000mm-1100mm. Return to the furnace and hold for 1-1.5h, then take it out of the furnace, and carry out a fire-drawing process with a pass reduction of 10mm-20mm to reach the diameter of the entire ingot Blanks are obtained by blanking. Cutting size is (height-to-diameter ratio is 1.84), return to the furnace for 1-1.5 hours; out of the furnace, upsetting to a height of H 650mm-700mm, return to the furnace for 1-1.5 hours. baked, adopted Punch punching, control the thickness of the punch material to 45mm-50mm, return to the furnace to cool down to the forming heating temperature of 1190°C-1210°C, and keep warm for 1-1.5...
Embodiment 2
[0038] The forging method of the Cr18Mn18N steel forging provided by the present embodiment comprises the following steps:
[0039] Forging blanking
[0040] The billet made of Cr18Mn18N steel is heated to the ingot heating temperature of 1230°C-1250°C, and then released from the furnace. Upsetting treatment to the height of the whole ingot H 1000mm, return to the furnace for 2.5-3h. Out of the furnace, the pass reduction is 10mm-15mm and pulled out to Return to the furnace to keep warm for 2-2.5h. Then out of the oven, the pass reduction is 30mm-50mm and pulled out to Blanks are obtained by blanking. Cutting size is (Height-to-diameter ratio is 1.99), return to the furnace for 1-5 hours; out of the furnace, upsetting to a height of H550mm-600mm, return to the furnace for 1-1.5 hours. baked, adopted Punch with a punch, control the thickness of the punch material to 50mm-60mm, return to the furnace to cool down to the forming heating temperature of 1200±10°C, and kee...
Embodiment 3
[0048] The forging method of the Cr18Mn18N steel forging provided by the present embodiment comprises the following steps:
[0049] Forging blanking
[0050] The billet made of Cr18Mn18N steel is heated and formed at a heating temperature of 1240°C-1260°C, out of the furnace, upsetting to the height of the whole ingot H 1000mm-1100mm, and returned to the furnace for 3-3.5h. Out of the furnace, the length of the pass is 10mm-20mm and the length is processed to Return to the furnace to keep warm for 3-3.5h. out of the oven, and then processed with a pass reduction of 20mm-30mm Blanking to obtain blanks, blanking: (The aspect ratio is 1.29), return to the furnace for 3-3.5h. Out of the furnace, the upsetting height H is 500mm-600mm, and it is returned to the furnace for 1-1.5h. baked, adopted Punch punching, control the thickness of the punch material to 40mm-50mm, return to the furnace to cool down to the ingot heating temperature of 1230±10°C, and keep warm for 3-3.5h...
PUM
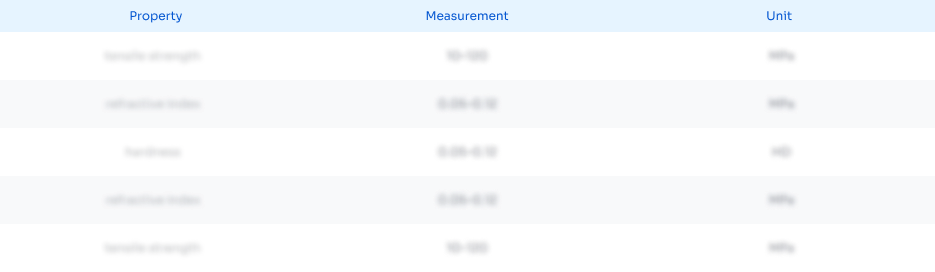
Abstract
Description
Claims
Application Information

- R&D
- Intellectual Property
- Life Sciences
- Materials
- Tech Scout
- Unparalleled Data Quality
- Higher Quality Content
- 60% Fewer Hallucinations
Browse by: Latest US Patents, China's latest patents, Technical Efficacy Thesaurus, Application Domain, Technology Topic, Popular Technical Reports.
© 2025 PatSnap. All rights reserved.Legal|Privacy policy|Modern Slavery Act Transparency Statement|Sitemap|About US| Contact US: help@patsnap.com