Low-density high-bearing sponge and manufacturing process
A high-load, low-density technology, applied in the sponge field, can solve problems such as unfavorable market competition, achieve the effects of reducing production costs, reducing production materials, and avoiding low density
- Summary
- Abstract
- Description
- Claims
- Application Information
AI Technical Summary
Problems solved by technology
Method used
Image
Examples
Embodiment 1
[0025] A production process of a low-density, high-load-bearing sponge includes the following steps: Step 1, weighing the material: Step 2, stirring the material: Step 3, heating and foaming: Step 4, curing and molding: Step 5, cutting and making the finished product: in:
[0026] In step 1, 167 parts of materials were weighed, including 35 parts of polyether polyol, 50 parts of polymer polyol, 15 parts of flame bonding agent, 0.37 parts of catalyst, 1.4 parts of silicone oil, 9.23 parts of foaming agent, and 56 parts of toluene diisocyanate. share.
[0027] In step 2, the materials in step 1 are fully stirred to obtain a mixture;
[0028] In step 3, the mixture in step 2 is placed in a foaming tank, and heated at 90-100°C for foaming, chain growth, and crosslinking to obtain a foamed mixture;
[0029] In step 4, put the foamed mixture in step 3 into a molding box to solidify to obtain a semi-finished product;
[0030] In step five, the semi-finished product in step four is...
Embodiment 2
[0032] A production process of a low-density, high-load-bearing sponge includes the following steps: Step 1, weighing the material: Step 2, stirring the material: Step 3, heating and foaming: Step 4, curing and molding: Step 5, cutting and making the finished product: in:
[0033] In step 1, 1000 parts of materials are weighed, including 220 parts of polyether polyol; 150 parts of polymer polyol; 90 parts of flame bonding agent; 1 part of catalyst; 14 parts of silicone oil; 75 parts of foaming agent; share;
[0034] In step 2, the materials in step 1 are fully stirred to obtain a mixture;
[0035] In step 3, the mixture in step 2 is placed in a foaming tank, and heated at 90-100°C for foaming, chain growth, and crosslinking to obtain a foamed mixture;
[0036] In step 4, put the foamed mixture in step 3 into a molding box to solidify to obtain a semi-finished product;
[0037] In step five, the semi-finished product in step four is cut to make a finished product.
Embodiment 3
[0039] A production process of a low-density, high-load-bearing sponge includes the following steps: Step 1, weighing the material: Step 2, stirring the material: Step 3, heating and foaming: Step 4, curing and molding: Step 5, cutting and making the finished product: in:
[0040] In step one, 100 parts of materials are weighed, including 54 parts of polyether polyol; 30 parts of polymer polyol; 24 parts of flame bonding agent; 0.9 parts of catalyst; 4.8 parts of silicone oil; share;
[0041] In step 2, the materials in step 1 are fully stirred to obtain a mixture;
[0042] In step 3, the mixture in step 2 is placed in a foaming tank, and heated at 90-100°C for foaming, chain growth, and crosslinking to obtain a foamed mixture;
[0043] In step 4, put the foamed mixture in step 3 into a molding box to solidify to obtain a semi-finished product;
[0044] In step five, the semi-finished product in step four is cut to make a finished product.
PUM
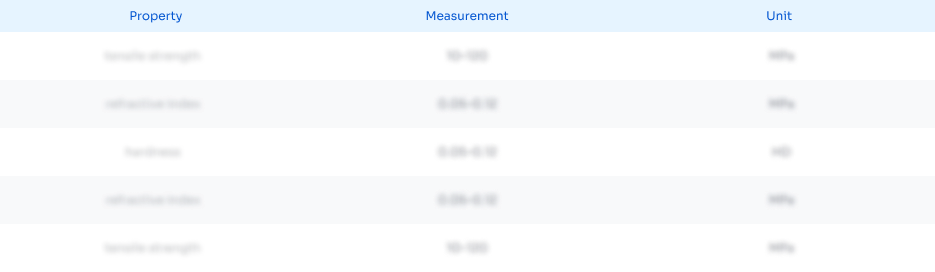
Abstract
Description
Claims
Application Information

- Generate Ideas
- Intellectual Property
- Life Sciences
- Materials
- Tech Scout
- Unparalleled Data Quality
- Higher Quality Content
- 60% Fewer Hallucinations
Browse by: Latest US Patents, China's latest patents, Technical Efficacy Thesaurus, Application Domain, Technology Topic, Popular Technical Reports.
© 2025 PatSnap. All rights reserved.Legal|Privacy policy|Modern Slavery Act Transparency Statement|Sitemap|About US| Contact US: help@patsnap.com