A Shape Optimization Method for 3D Product Model
A product model and optimization method technology, applied in 3D modeling, instrumentation, calculation, etc., can solve the problems of irregular optimization boundary, time-consuming and laborious grid division, and reduced optimization efficiency, so as to reduce design variables, improve calculation efficiency, The effect of convenient interaction
- Summary
- Abstract
- Description
- Claims
- Application Information
AI Technical Summary
Problems solved by technology
Method used
Image
Examples
experiment example 1
[0076] Experimental example 1: Shape optimization of a ridged cantilever
[0077] The shape optimization method includes the following steps:
[0078] Step 1. Establish a characteristic frame model of a ridged cantilever beam, such as image 3 (a) and image 3 As shown in (b), the characteristic dimensions of the characteristic frame model include the width W of the ridge, the height H of the ridge, the overall thickness t, and the length L of the ridge, such as image 3 As shown in (c), the load of the model is Z=0, the end face is uniformly pulled along the negative direction of the y-axis, F=-50N, and the boundary condition is that the end face is completely fixed;
[0079] Step 2: Obtain the coordinate matrix of the parameterized control point of the cantilever ridge according to equations (18)~(21):
[0080]
[0081] Where x 0 Is the x coordinate of the ridge vertex, x 1 Is the x coordinate of the control point on the ridge, x 1 ′ Is the updated x 1 , W 0 Is the vertex ridge width...
experiment example 2
[0099] Experimental example 2: The shape optimization method of the dredging cutter arm
[0100] Step 1. Establish the characteristic frame model of the dredging cutter arm, such as Figure 5 As shown, the characteristic dimensions of the characteristic frame model include the axial width bW and the axial length bL of the lower bottom surface of the reamer arm, the axial width tW and the axial length tL of the upper top surface, the height of the reamer arm H, and the load and boundary conditions are : The upper and lower bottom surfaces of the reamer arm are fixedly restrained, and a concentrated force is applied at the designated control point.
[0101] Step 2. When the feature size type is length, the mapping function is derived. Let any two points in the space be (x 0 ,y 0 ,z 0 ) And (x 1 ,y 1 ,z 1 ), the feature size along the X-axis, Y-axis, and Z-axis is determined by W 0 ,L 0 ,H 0 Change to W, L, H, change (x 0 ,y 0 ,z 0 ) As a fixed point, set a moving point (x 1 ,y 1 ,z 1...
PUM
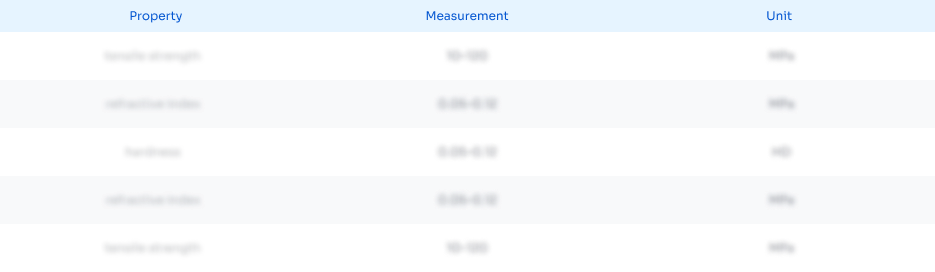
Abstract
Description
Claims
Application Information

- Generate Ideas
- Intellectual Property
- Life Sciences
- Materials
- Tech Scout
- Unparalleled Data Quality
- Higher Quality Content
- 60% Fewer Hallucinations
Browse by: Latest US Patents, China's latest patents, Technical Efficacy Thesaurus, Application Domain, Technology Topic, Popular Technical Reports.
© 2025 PatSnap. All rights reserved.Legal|Privacy policy|Modern Slavery Act Transparency Statement|Sitemap|About US| Contact US: help@patsnap.com