Method for preparing briquette binder from kitchen waste and cattle manure
A technology of kitchen waste and binder, which is applied in the petroleum industry, solid fuel, fuel, etc., can solve the problems of poor thermal strength and thermal stability, increase and decrease the ash content of briquette coal, and achieve thermal state Excellent strength and thermal stability, improved adhesion, fast water evaporation effect
- Summary
- Abstract
- Description
- Claims
- Application Information
AI Technical Summary
Problems solved by technology
Method used
Examples
example 1
[0015] First recover 3kg of leftovers in the kitchen, filter them, collect the filter residue, put the filter residue into the container, then add 20g of sodium humate and 8g of bentonite, stir and mix for 10min, then weigh 200g of corn stalks, and crush them After forming slag, add it to the above container, stir and mix for 20 minutes to obtain the mixture; weigh 100g of distiller's grains and add it to the above container, stir and mix evenly, pour it into the fermenter, and ferment at 35°C for 3 days, then place the fermented product in In a centrifuge, centrifuge at 4000r / min for 30min, collect the supernatant and sediment respectively, freeze-dry the supernatant, collect the dried matter, mix the dried matter with the sediment to obtain a mixture, and set aside; weigh 1kg of cattle Feces and 300g of peanut shells were placed in an oven, dried at 90°C until the moisture content was 20%, then placed in a pulverizer for 20 minutes, and then placed in a container, then the bi...
example 2
[0018] First recover 5kg of leftovers in the kitchen, filter them, collect the filter residue, put the filter residue into the container, then add 30g of sodium humate and 12g of bentonite, stir and mix for 20min, then weigh 300g of corn stalks, and crush them After forming slag, add it to the above container, stir and mix for 30 minutes to obtain the mixture; weigh 200g distiller's grains and add it to the above container, stir and mix evenly, pour it into the fermenter, and ferment at 45°C for 5 days, then place the fermented product in In a centrifuge, centrifuge at 5000r / min for 40min, collect the supernatant and sediment respectively, freeze-dry the supernatant, collect the dried matter, mix the dried matter with the sediment to obtain a mixture, and set aside; weigh 2kg cattle Feces and 400g of peanut shells were placed in an oven, dried at 100°C until the moisture content was 30%, then placed in a pulverizer for 25 minutes, and then placed in a container, then the biogas...
example 3
[0021] First recover 4kg of leftovers in the kitchen, filter them, collect the filter residue, put the filter residue into the container, then add 25g of sodium humate and 10g of bentonite, stir and mix for 15min, then weigh 250g of corn stalks, and crush them After forming slag, add it to the above container, stir and mix for 25 minutes to obtain the mixture; weigh 150g of distiller's grains and add it to the above container, stir and mix evenly, pour it into the fermenter, and ferment at 40°C for 4 days, then place the fermented product in In a centrifuge, centrifuge at 4500r / min for 35min, collect the supernatant and sediment respectively, freeze-dry the supernatant, collect the dried matter, mix the dried matter with the sediment to obtain a mixture, and set aside; weigh 1.5kg Cow dung and 350g peanut shells were placed in an oven, dried at 95°C until the moisture content was 25%, then placed in a pulverizer for 30 minutes, and then placed in a container, then the biogas liqu...
PUM
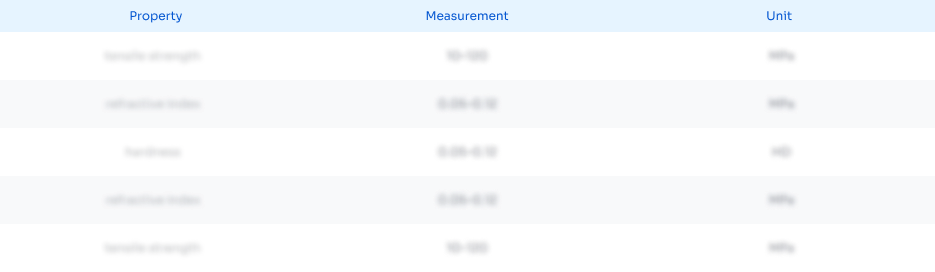
Abstract
Description
Claims
Application Information

- Generate Ideas
- Intellectual Property
- Life Sciences
- Materials
- Tech Scout
- Unparalleled Data Quality
- Higher Quality Content
- 60% Fewer Hallucinations
Browse by: Latest US Patents, China's latest patents, Technical Efficacy Thesaurus, Application Domain, Technology Topic, Popular Technical Reports.
© 2025 PatSnap. All rights reserved.Legal|Privacy policy|Modern Slavery Act Transparency Statement|Sitemap|About US| Contact US: help@patsnap.com