Novel membrane transfer-printing process
A film and process technology, applied in the field of new film transfer process, can solve problems such as easy warping and deformation of products, achieve consistent shrinkage, reduce sheet pre-forming processes, and high efficiency
- Summary
- Abstract
- Description
- Claims
- Application Information
AI Technical Summary
Problems solved by technology
Method used
Examples
Embodiment 1
[0018] A novel membrane transfer printing process, comprising the following steps:
[0019] 1), PET pretreatment, coating printing release layer;
[0020] The method for PET pretreatment comprises the following steps:
[0021] 1) Soak the surface of PET substrate with wetting solution for 4 minutes, and wash with purified water;
[0022] 2) Soak in sediment solution for 4 minutes, wash with purified water;
[0023] 3) Soak in the conductive film working solution for 6 minutes to deposit the conductive film, control pH3, and wash with purified water.
[0024] 2), printing pattern and varnish adhesive; the varnish adhesive includes the following raw materials in parts by weight: 3 parts of antistatic agent, 40 parts of polyurethane acrylate, 30 parts of acrylate monomer, and 5 parts of unsaturated polyester , 1 part of photoinitiator, 5 parts of crosslinking agent, 2 parts of coupling agent.
[0025] 3) Injection molding The injection molding method is roll material.
Embodiment 2
[0027] A novel membrane transfer printing process, comprising the following steps:
[0028] 1), PET pretreatment, coating printing release layer;
[0029] The method for PET pretreatment comprises the following steps:
[0030] 1) Soak the surface of PET substrate with wetting solution for 6 minutes, and wash with purified water;
[0031] 2) Soak in sediment solution for 5 minutes, wash with purified water;
[0032] 3) Soak in the conductive film working solution for 8 minutes to deposit the conductive film, control the pH to 4, and wash with purified water.
[0033] 2), printing pattern and varnish adhesive; varnish adhesive includes the following raw materials in parts by weight: 3 parts of antistatic agent, 40 parts of polyurethane acrylate, 50 parts of acrylate monomer, and 8 parts of unsaturated polyester , 1 part of photoinitiator, 5 parts of crosslinking agent, 5 parts of coupling agent.
[0034] 3) Injection molding The injection molding method is sheet material.
Embodiment 3
[0036] A novel membrane transfer printing process, comprising the following steps:
[0037] 1), PET pretreatment, coating printing release layer;
[0038] The method for PET pretreatment comprises the following steps:
[0039] 1) Soak the surface of the PET substrate with a wetting solution for 5 minutes, and wash with purified water;
[0040] 2) Soak in sediment solution for 4.5 minutes, wash with purified water;
[0041] 3) Soak in the conductive film working solution for 7 minutes to deposit the conductive film, control the pH to 3.5, and wash with purified water.
[0042] 2), printing pattern and varnish adhesive; the varnish adhesive includes the following raw materials in parts by weight: 3 parts of antistatic agent, 40 parts of polyurethane acrylate, 40 parts of acrylate monomer, and 7 parts of unsaturated polyester , 1 part of photoinitiator, 5 parts of crosslinking agent, 3 parts of coupling agent.
[0043] 3) Injection molding The injection molding method is shee...
PUM
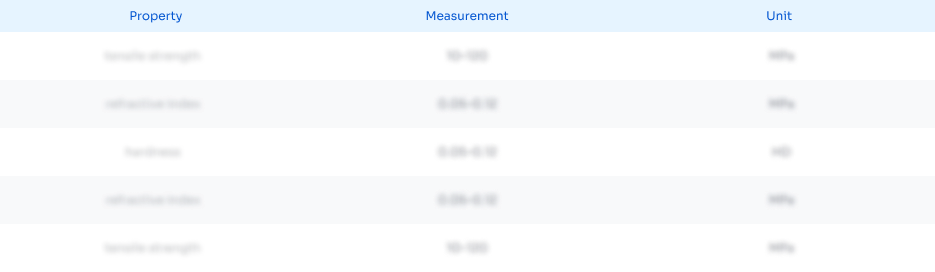
Abstract
Description
Claims
Application Information

- R&D
- Intellectual Property
- Life Sciences
- Materials
- Tech Scout
- Unparalleled Data Quality
- Higher Quality Content
- 60% Fewer Hallucinations
Browse by: Latest US Patents, China's latest patents, Technical Efficacy Thesaurus, Application Domain, Technology Topic, Popular Technical Reports.
© 2025 PatSnap. All rights reserved.Legal|Privacy policy|Modern Slavery Act Transparency Statement|Sitemap|About US| Contact US: help@patsnap.com