A configuration method of raw slurry in the process of producing alumina by sintering method
A configuration method and alumina technology, applied in the field of metallurgy, can solve the problems of difficulty in controlling the moisture content of raw slurry, a large number of blending tanks, and a low pass rate of indicators, so as to reduce the number of blending tanks and the number of pouring tanks, and reduce operation and maintenance costs , The preparation process is short and effective
- Summary
- Abstract
- Description
- Claims
- Application Information
AI Technical Summary
Problems solved by technology
Method used
Examples
Embodiment 1
[0025] 1) Wet material slurry: pump the carbon separation mother liquor and silicon slag slurry into the mixing tank, and introduce the desiliconized fly ash filter cake into the mixing tank through the flow tank, and continuously mix until uniform under the condition of stirring. Use a pump to introduce the mixed wet material into the storage tank with a flow rate of 100m 3 / h, adjust the alkali ratio of the wet material after pulping to 0.95, and the moisture content of the wet material to 55%;
[0026] 2) Dry material grinding: add limestone, quicklime, anthracite, bauxite, etc. into the vertical mill for drying, grinding, mixing, and then enter the homogenization store to obtain dry powder;
[0027] 3) Mix the ingredients, put the dry powder in the homogenization warehouse into the mixer at a speed of 36.2t / h with a screw feeding scale, and mix evenly with the wet material after pulping under stirring conditions to obtain a mixture, and adjust the content of the mixture C...
Embodiment 2
[0030] 1) Wet material slurry: pump the carbon separation mother liquor and silicon slag slurry into the slurry tank, transfer the desiliconized fly ash filter cake into the slurry tank through the chute, and keep mixing until uniform under the condition of stirring. After homogenization, use a pump to introduce the mixed wet material into the mixing tank with a flow rate of 100m 3 / h, the moisture content of the wet material is 55%; adjust the alkali ratio of the wet material after pulping to 1.05;
[0031] 2) Dry material grinding: add limestone, quicklime, anthracite, bauxite, etc. into the vertical mill for drying, grinding, mixing, and then enter the homogenization store to obtain dry powder;
[0032] 3) For mixing ingredients, the dry powder in the homogenization warehouse is transported by screw metering, and is added to the mixing tank at a speed of 43.71t / h, and mixed with the wet material after slurrying under stirring conditions to obtain a mixture, and the mixture ...
PUM
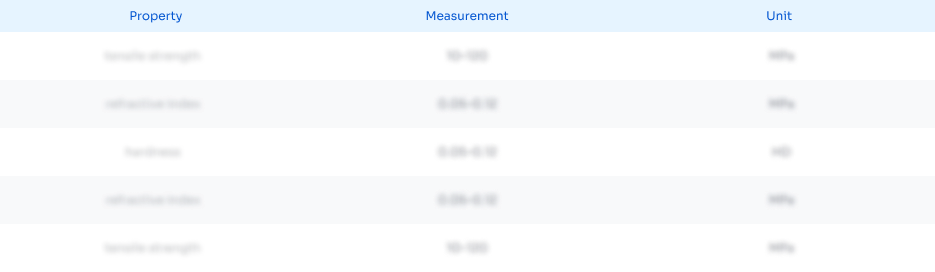
Abstract
Description
Claims
Application Information

- Generate Ideas
- Intellectual Property
- Life Sciences
- Materials
- Tech Scout
- Unparalleled Data Quality
- Higher Quality Content
- 60% Fewer Hallucinations
Browse by: Latest US Patents, China's latest patents, Technical Efficacy Thesaurus, Application Domain, Technology Topic, Popular Technical Reports.
© 2025 PatSnap. All rights reserved.Legal|Privacy policy|Modern Slavery Act Transparency Statement|Sitemap|About US| Contact US: help@patsnap.com