Integral molding process of transformer oil conservator capsule
A technology of integral molding and molding process, which is applied to household appliances, other household appliances, household components, etc., can solve the problem that the chemical properties and physical size consistency of the adhesive tape cannot be effectively guaranteed, the consistency of the capsule and the long-term operation reliability are affected, and the capsule is affected. Air tightness and pressure resistance performance, etc., to ensure consistency and long-term operation reliability, eliminate hidden dangers of pollution, and uniform pressure
- Summary
- Abstract
- Description
- Claims
- Application Information
AI Technical Summary
Problems solved by technology
Method used
Image
Examples
Embodiment 1
[0024] In this embodiment, the specification is 234×124mm. The overall molding process of the transformer oil conservator capsule is changed from the production process of single-sided calendered adhesive tape to the production process of double-sided calendered adhesive tape, and the molding and vulcanization are combined. The specific steps are as follows:
[0025] (1) Preparation of the first rubber material and the second rubber material: Roughly knead the mixed gel A on the open mixer, and then refine it to make it fully mixed evenly and remove air bubbles, and then make small rolls. Form the first rubber material of the whole roll; roughen the mixed gel B on the open mill first, and then refine it to make it fully mixed evenly and remove air bubbles, and then make small rolls to form the first rubber material of the whole roll. Two rubber materials;
[0026] (2) Double-sided calendering:
[0027] The first step is to carry out front calendering of the base fabric, put t...
Embodiment 2
[0039] Compared with Embodiment 1, this embodiment changes the size of the capsule of the transformer oil conservator to 306×254 mm, and its overall molding process remains unchanged.
[0040] In order to compare the performance of the capsule product of transformer oil conservator in this example, it was compared with the capsule product of transformer oil conservator of the same specification prepared by three manufacturers in the market. The comparison results are shown in Table 2:
[0041]
[0042] Note: For the air tightness test, slowly fill the capsule with compressed air at room temperature and in an unconstrained state, park it for 20 minutes to stabilize the pressure to 1.0KPa±0.01 KPa, soak it in water or apply soapy water on its surface, and observe whether there is any bubble.
[0043] It can be seen from the above table that through the implementation method of this example, the comprehensive performance of the prepared transformer oil conservator capsule prod...
Embodiment 3
[0045] Compared with Embodiment 1, this embodiment changes the size of the capsule of the transformer oil conservator to 228×114 mm, and its overall molding process remains unchanged.
[0046] In order to compare the performance of the capsule product of transformer oil conservator in this example, it was compared with the capsule product of transformer oil conservator of the same specification prepared by three manufacturers in the market. The comparison results are shown in Table 3:
[0047]
[0048] Note: For the air tightness test, slowly fill the capsule with compressed air at room temperature and in an unconstrained state, park it for 20 minutes to stabilize the pressure to 1.0KPa±0.01 KPa, soak it in water or apply soapy water on its surface, and observe whether there is any bubble.
[0049] It can be seen from the above table that through the implementation method of this example, the comprehensive performance of the prepared transformer oil conservator capsule prod...
PUM
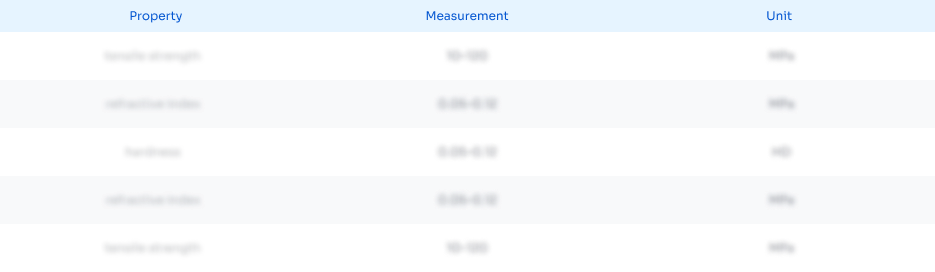
Abstract
Description
Claims
Application Information

- Generate Ideas
- Intellectual Property
- Life Sciences
- Materials
- Tech Scout
- Unparalleled Data Quality
- Higher Quality Content
- 60% Fewer Hallucinations
Browse by: Latest US Patents, China's latest patents, Technical Efficacy Thesaurus, Application Domain, Technology Topic, Popular Technical Reports.
© 2025 PatSnap. All rights reserved.Legal|Privacy policy|Modern Slavery Act Transparency Statement|Sitemap|About US| Contact US: help@patsnap.com