Machining process for double-layer composite metallic tube
A double-layer composite and processing technology, which is applied in the field of metal double-layer composite pipe processing technology, can solve the problems of difficult to guarantee processing quality, high product scrap rate, low profit margin, etc., to reduce product scrap rate and optimize processing The effect of simple process and processing technology
- Summary
- Abstract
- Description
- Claims
- Application Information
AI Technical Summary
Problems solved by technology
Method used
Image
Examples
Embodiment Construction
[0022] The present invention will be further described below in conjunction with the accompanying drawings.
[0023] A kind of processing technology of metal double-layer composite pipe, this technology comprises the following steps:
[0024] The first step is to select the metal outer tube 1 and the metal inner tube 2 to be processed so that the length of the metal outer tube 1 is greater than the length of the metal inner tube 2, and insert the metal inner tube 2 into the inside of the metal outer tube 1;
[0025] In the second step, sealing plugs 3 are installed at both ends of the metal outer tube 1;
[0026] The third step is to select the inner tube forming die 4, the inner tube model cavity 41 of the inner tube forming die 4 is consistent with the shape of the outer wall of the metal inner tube 2 after forming; the metal outer tube 1 and the metal inner tube 2 that are socketed together are placed into the inner tube mold cavity 41, see figure 1 ;
[0027] The fourth...
PUM
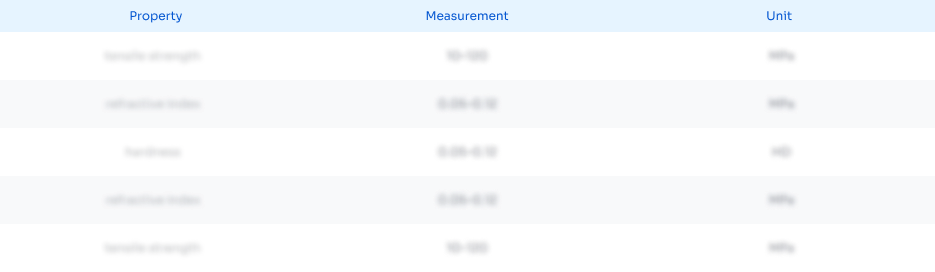
Abstract
Description
Claims
Application Information

- Generate Ideas
- Intellectual Property
- Life Sciences
- Materials
- Tech Scout
- Unparalleled Data Quality
- Higher Quality Content
- 60% Fewer Hallucinations
Browse by: Latest US Patents, China's latest patents, Technical Efficacy Thesaurus, Application Domain, Technology Topic, Popular Technical Reports.
© 2025 PatSnap. All rights reserved.Legal|Privacy policy|Modern Slavery Act Transparency Statement|Sitemap|About US| Contact US: help@patsnap.com