Preparation method for polishing solution of stainless steel part
A polishing liquid and stainless steel technology, applied in the direction of polishing composition containing abrasives, etc., can solve the problems of uneven and smooth surface, deep damage layer, error, etc., achieve good polishing effect, environmental protection and pollution-free raw materials, and no damage to the surface Effect
- Summary
- Abstract
- Description
- Claims
- Application Information
AI Technical Summary
Problems solved by technology
Method used
Examples
Embodiment 1
[0013] A preparation method for a polishing solution for stainless steel parts, comprising the following specific steps:
[0014] 1) Weigh each raw material according to the following ratio by weight percentage: 2.2% chromium carbide; 0.6% zirconium dioxide; 1.5% muscovite; 3% calcium aluminate; 2.8% 1,2,3-benzotriazole; Sodium cetyl sulfonate 3%; cubic boron nitride 3%; lignocellulose 3.5%; silicon carbide 2%; simethicone 1.2%; the balance is water;
[0015] 2) Grind chromium carbide to an average particle size of 0.05 microns, zirconia to an average particle size of 0.1 microns, muscovite to an average particle size of 5 microns, calcium aluminate to an average particle size of 20 nanometers, and cubic boron nitride Grinding to an average particle size of 0.2 microns, grinding silicon carbide to an average particle size of 1.2 microns and mixing uniformly to obtain a mixed powder;
[0016] 3) Mix and heat 1,2,3-benzotriazole, sodium hexadecylsulfonate, lignocellulose, simet...
Embodiment 2
[0018] A preparation method for a polishing solution for stainless steel parts, comprising the following specific steps:
[0019] 1) Weigh each raw material according to the following ratio by weight percentage: 2.2% chromium carbide; 0.5% zirconium dioxide; 1.7% muscovite; 3.5% calcium aluminate; 2.6% 1,2,3-benzotriazole; Sodium cetyl sulfonate 3%; cubic boron nitride 2.8%; lignocellulose 3.5%; silicon carbide 5%; simethicone 1.2%; the balance is water;
[0020] 2) Grind chromium carbide to an average particle size of 0.08 microns, zirconia to an average particle size of 0.1 microns, muscovite to an average particle size of 5 microns, calcium aluminate to an average particle size of 20 nanometers, and cubic boron nitride Grinding to an average particle size of 0.2 microns, grinding silicon carbide to an average particle size of 1.2 microns and mixing uniformly to obtain a mixed powder;
[0021] 3) Mix and heat 1,2,3-benzotriazole, sodium hexadecylsulfonate, lignocellulose, s...
Embodiment 3
[0023] A preparation method for a polishing solution for stainless steel parts, comprising the following specific steps:
[0024] 1) Weigh each raw material according to the following ratio by weight percentage: 2.2% chromium carbide; 0.3% zirconium dioxide; 1.6% muscovite; 3% calcium aluminate; 2.8% 1,2,3-benzotriazole; Sodium cetyl sulfonate 2%; cubic boron nitride 2.8%; lignocellulose 2.5%; silicon carbide 2%; simethicone 1.2%; the balance is water.
[0025] 2) Grind chromium carbide to an average particle size of 0.05 microns, zirconia to an average particle size of 0.1 microns, muscovite to an average particle size of 2 microns, calcium aluminate to an average particle size of 15 nanometers, and cubic boron nitride Grinding to an average particle size of 0.2 microns, grinding silicon carbide to an average particle size of 1.2 microns and mixing uniformly to obtain a mixed powder;
[0026] 3) Mix and heat 1,2,3-benzotriazole, sodium hexadecylsulfonate, lignocellulose, sim...
PUM
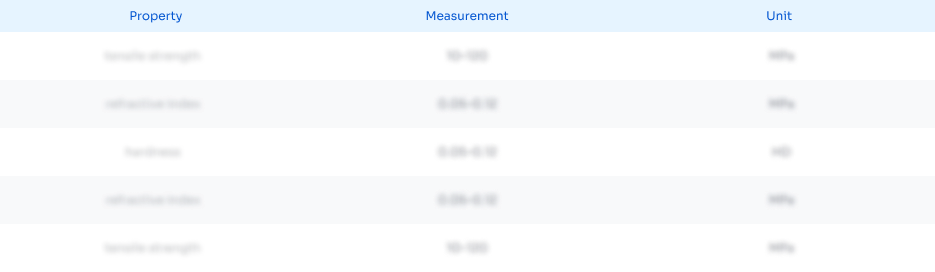
Abstract
Description
Claims
Application Information

- R&D
- Intellectual Property
- Life Sciences
- Materials
- Tech Scout
- Unparalleled Data Quality
- Higher Quality Content
- 60% Fewer Hallucinations
Browse by: Latest US Patents, China's latest patents, Technical Efficacy Thesaurus, Application Domain, Technology Topic, Popular Technical Reports.
© 2025 PatSnap. All rights reserved.Legal|Privacy policy|Modern Slavery Act Transparency Statement|Sitemap|About US| Contact US: help@patsnap.com