Environment-friendly plastic runway material and preparation method thereof
A plastic track and environmental protection technology, applied in the field of sports equipment materials, can solve the problem of volatilization of harmful gases from the plastic track, and achieve the effects of good mechanical properties, appropriate elasticity and convenient production.
- Summary
- Abstract
- Description
- Claims
- Application Information
AI Technical Summary
Problems solved by technology
Method used
Image
Examples
Embodiment 1
[0035] The preparation method of the environment-friendly plastic runway material provided by the present embodiment specifically comprises the following steps:
[0036] (1) Preparation of component A: Stir 500kg of polyether diol for 10 minutes, add 180kg of liquefied MDI, raise the temperature to 80-85°C, and perform a free reaction. Start timing from the temperature rise to 80°C for 2 hours and then add 180kg MDI, mix well, cool down to 70°C and add 250kg chlorinated palm oil methyl ester, mix well to obtain component A;
[0037] (2), preparation of component B: 280kg polyether diol, 40kgMOCA and 20kg ferric chloride red are mixed and ground, then add 180kg polyether triol, 400kg chlorinated palm oil methyl ester and 70kg talcum powder in sequence , the temperature was raised to 78°C for 1.5 hours to carry out the vacuum reaction to obtain component B;
[0038] (3), after mixing component A prepared in step (1) and component B prepared in step (2) according to a mass ratio...
Embodiment 2
[0040] (1) Preparation of component A: Stir 540kg of polyether N220 for 20 minutes, then add 220kg of liquefied MDI-100LL, heat up to 80-85°C for free reaction, start timing for 2.5 hours from the temperature rise to 80°C, and then add 220kg MDI50, mix well, cool down to 75°C and add 290kg chlorinated palm oil methyl ester, mix well to get component A;
[0041] (2), preparation of component B: 320kg polyether N220, 60kg MOCA and 30kg ferric chloride red are mixed and ground, then 220kg polyether 330N, 500kg chlorinated palm oil methyl ester and 80kg talcum powder are added successively, and the temperature is raised to 83°C Carry out 2.0 hours vacuum reaction, obtain component B;
[0042](3) After mixing component A prepared in step (1) and component B prepared in step (2) according to a mass ratio of 1:(3~5), add component A and component B Divide the mass of B and 0.1% to 0.5% of the curing agent DY-20, stir and shape, and then the environmentally friendly plastic track mat...
Embodiment 3
[0044] (1) Preparation of component A: Stir 520kg of polyether N220 for 15 minutes, add 200kg of liquefied MDI-100LL, raise the temperature to 80-85°C, and carry out free reaction, start timing from the temperature rise to 80°C for 2 hours, then add 200kg MDI50, mix well and cool down to 70°C and add 250kg chlorinated palm oil methyl ester, mix well to obtain component A;
[0045] (2), preparation of component B: 300kg polyether N220, 50kg MOCA and 25kg ferric chloride red are mixed and ground, then 200kg polyether 330N, 450kg chlorinated palm oil methyl ester and 75kg talcum powder are added successively, and the temperature is raised to 80°C Carry out 2.0 hours vacuum reaction, obtain component B;
[0046] (3), after mixing component A prepared in step (1) and component B prepared in step (2) according to a mass ratio of 1:4, add component A and component B mass and 0.3% of the curing agent DY-20, stirring and finalizing, you can get the environmental protection plastic run...
PUM
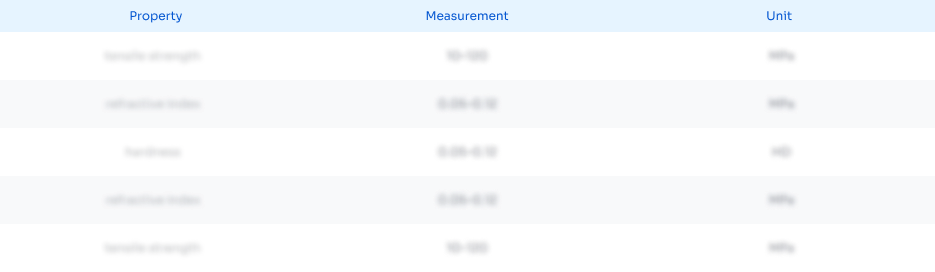
Abstract
Description
Claims
Application Information

- Generate Ideas
- Intellectual Property
- Life Sciences
- Materials
- Tech Scout
- Unparalleled Data Quality
- Higher Quality Content
- 60% Fewer Hallucinations
Browse by: Latest US Patents, China's latest patents, Technical Efficacy Thesaurus, Application Domain, Technology Topic, Popular Technical Reports.
© 2025 PatSnap. All rights reserved.Legal|Privacy policy|Modern Slavery Act Transparency Statement|Sitemap|About US| Contact US: help@patsnap.com