Wheel hub mounting hole flexible and automatic machining system based on machine vision
An automatic processing and machine vision technology, applied in general control systems, control/adjustment systems, instruments, etc., can solve problems such as the limitation of artificial wheel hub processing efficiency
- Summary
- Abstract
- Description
- Claims
- Application Information
AI Technical Summary
Problems solved by technology
Method used
Image
Examples
Embodiment 1
[0033] see Figure 1-7 As shown, the present invention provides a flexible automatic processing system for hub mounting holes based on machine vision, including a conveying system 1, an automatic loading and unloading system 5, a processing system 7, a positioning system 3, a vision system and a pouring and returning system 4; the conveying system 1 is an upper and lower two-layer structure fixed on the conveyor frame 103, the upper layer structure is the feeding layer 101, and the lower layer structure is the return layer 102, and the feeding layer 101 and the return layer 102 include several feeding rollers arranged on the conveyor frame 103 104, the two ends of feeding drum 104 are all provided with some sprockets, and the conveyer frame 103 is also provided with the driving motor 105 that is connected with chain wheels by chain; Moreover, the reflow layer 102 passes under the loading and unloading guide rail 502 and corresponds to the position of the pouring backflow syste...
Embodiment 2
[0041] see Figure 8-10 As shown, the difference between embodiment 2 and embodiment 1 is:
[0042] The automatic loading and unloading system 5 includes a first loading and unloading guide rail 511 and two second loading and unloading guide rails 512 arranged on the loading and unloading frame, and a first clamping device 503 arranged on the first loading and unloading guide rail 511 through a connecting plate, The second loading and unloading guide rail 512 and the first loading and unloading guide rail 511 form an "H"-shaped structure, and the processing system 7 is four CNC numerical control processing machine tools, which are distributed on both sides of the automatic loading and unloading system 5 .
PUM
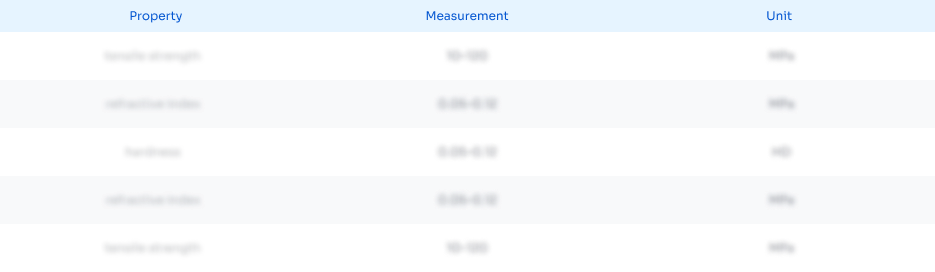
Abstract
Description
Claims
Application Information

- R&D Engineer
- R&D Manager
- IP Professional
- Industry Leading Data Capabilities
- Powerful AI technology
- Patent DNA Extraction
Browse by: Latest US Patents, China's latest patents, Technical Efficacy Thesaurus, Application Domain, Technology Topic, Popular Technical Reports.
© 2024 PatSnap. All rights reserved.Legal|Privacy policy|Modern Slavery Act Transparency Statement|Sitemap|About US| Contact US: help@patsnap.com