Black glass fiber reinforced nylon 6 material for laser welding and preparing method thereof
A laser welding and nylon technology, applied in the field of black glass fiber reinforced nylon 6 material and its preparation, can solve the problems of low strength of thick-walled parts, no laser permeability, long welding cycle, etc. , the effect of shortening the welding cycle
- Summary
- Abstract
- Description
- Claims
- Application Information
AI Technical Summary
Problems solved by technology
Method used
Image
Examples
Embodiment 1
[0028] Weigh 6.4kg of component A, 0.5kg of component C2, and 0.1kg of component D, and mix them with a high-speed mixer, then melt and extrude them with 3kg of component B2 flat glass fibers fed from the side through a twin-screw extruder , and then pelletized by a granulator, and the resulting pellets were dried in an oven at 90°C for 4 hours, and then obtained by injection molding with an injection molding machine; the speed of the high-speed mixer was set at 1400r / min, and the temperature of the extruder was set at 200-280°C , The temperature of the injection molding machine is set at 280°C, and the injection pressure is 70-120bar.
Embodiment 2
[0030] Weigh respectively 2.5kg of component A, 2kg of component C2, and 0.5kg of component D. After mixing with a high-speed mixer, melt and extrude them with 5kg of component B2 flat glass fibers fed from the side through a twin-screw extruder. Then pelletized by a granulator, the resulting pellets were dried in an oven at 90°C for 4 hours, and then obtained by injection molding with an injection molding machine; the speed of the high-speed mixer was set at 1400r / min, and the temperature of the extruder was set at 200-280°C. The temperature of the injection molding machine is set to 280° C., and the injection pressure is 70 to 120 bar.
Embodiment 3
[0032] Weigh 8.5kg of component A, 0.1kg of component C2, and 0.4kg of component D, and mix them with a high-speed mixer, then melt and extrude them with 1kg of component B2 flat glass fiber fed from the side through a twin-screw extruder , and then pelletized by a granulator, and the resulting pellets were dried in an oven at 90°C for 4 hours, and then obtained by injection molding with an injection molding machine; the speed of the high-speed mixer was set at 1400r / min, and the temperature of the extruder was set at 200-280°C , The temperature of the injection molding machine is set at 280°C, and the injection pressure is 70-120bar.
PUM
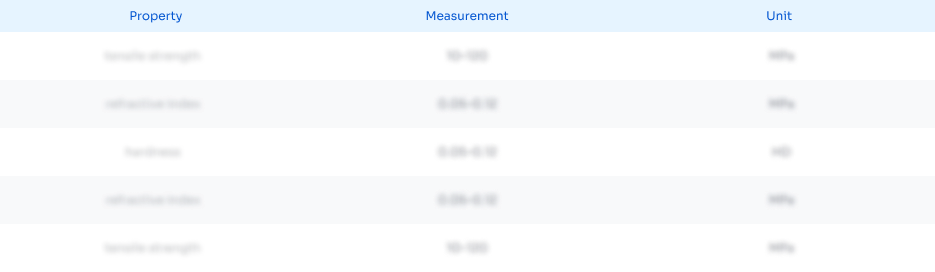
Abstract
Description
Claims
Application Information

- R&D Engineer
- R&D Manager
- IP Professional
- Industry Leading Data Capabilities
- Powerful AI technology
- Patent DNA Extraction
Browse by: Latest US Patents, China's latest patents, Technical Efficacy Thesaurus, Application Domain, Technology Topic.
© 2024 PatSnap. All rights reserved.Legal|Privacy policy|Modern Slavery Act Transparency Statement|Sitemap