Thermosetting modified polystyrene board and its production process
A polystyrene board, thermosetting technology, applied in the field of construction, can solve the problems of fire, the cavity generated by the thermal insulation system, and the poor fire resistance of the polystyrene board, so as to prolong the life of the building, reduce the maintenance cost and prolong the service life.
- Summary
- Abstract
- Description
- Claims
- Application Information
AI Technical Summary
Problems solved by technology
Method used
Examples
Embodiment 1
[0024] A thermosetting modified polystyrene board includes the following raw materials in parts by weight: 800 kg of polystyrene particles, 80 kg of cement, 8 kg of rubber powder, 1 kg of polypropylene fiber, 45 kg of magnesium carbonate, 1 kg of sodium stearate and 550 kg of water.
[0025] The production process of the thermosetting modified polystyrene board includes the following steps:
[0026] (1) Stir the polystyrene particles, cement, rubber powder, polypropylene fiber, sodium stearate and water at a stirring speed of 100r / min for 10 minutes to mix and stir to obtain a mixed solution A;
[0027] (2) Add magnesium carbonate to mixed liquid A, and mix and stir for 10 minutes at a stirring speed of 1200r / min under the condition of heating temperature of 55°C to obtain mixed liquid B;
[0028] (3) Molding the mixed solution B into the thermosetting modified polystyrene board. The thermosetting modified polystyrene board of the present invention adopts heating conditions, adding po...
Embodiment 2
[0030] A thermosetting modified polystyrene board, comprising the following parts by weight of raw materials: polystyrene particles 1000kg, cement 100kg, rubber powder 10kg, polypropylene fiber 2kg, 50kg of a mixture of zinc carbonate and calcium carbonate in any ratio, calcium stearate and A mixture of 2kg of aluminum stearate and 600kg of water in any ratio.
[0031] The production process of the thermosetting modified polystyrene board includes the following steps:
[0032] (1) Stir the polystyrene particles, cement, rubber powder, polypropylene fiber, calcium stearate, aluminum stearate and water at a stirring speed of 150r / min for 15 minutes and mix and stir to obtain a mixed solution A;
[0033] (2) Add zinc carbonate and calcium carbonate to mixed solution A, and mix and stir for 15 minutes at a stirring speed of 1400r / min at a heating temperature of 60°C to obtain mixed solution B;
[0034] (3) The thermosetting modified polystyrene board is molded by casting the mixed solutio...
Embodiment 3
[0036] A thermosetting modified polystyrene board, comprising the following raw materials in parts by weight: 1200kg of polystyrene particles, 120kg of cement, 12kg of rubber powder, 3kg of polypropylene fiber, 55kg of a mixture of magnesium carbonate, zinc carbonate and calcium carbonate in any proportion, and stearin A mixture of 3kg of aluminum acid and sodium methyl silicate in any ratio and 650kg of water.
[0037] The production process of the thermosetting modified polystyrene board includes the following steps:
[0038] (1) Stir the polyphenyl particles, cement, rubber powder, polypropylene fiber, aluminum stearate, sodium methyl silicate and water at a stirring speed of 200r / min for 20 minutes and mix and stir to obtain a mixed solution A;
[0039] (2) Add magnesium carbonate, zinc carbonate and calcium carbonate to mixed solution A, and mix and stir for 20 minutes at a stirring speed of 1600r / min under the condition of heating temperature of 65°C to obtain mixed solution B;...
PUM
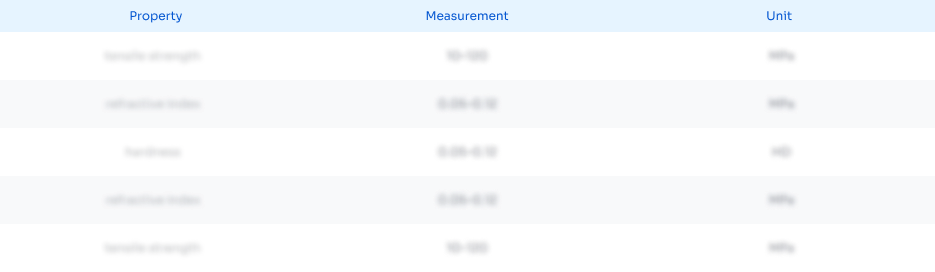
Abstract
Description
Claims
Application Information

- R&D
- Intellectual Property
- Life Sciences
- Materials
- Tech Scout
- Unparalleled Data Quality
- Higher Quality Content
- 60% Fewer Hallucinations
Browse by: Latest US Patents, China's latest patents, Technical Efficacy Thesaurus, Application Domain, Technology Topic, Popular Technical Reports.
© 2025 PatSnap. All rights reserved.Legal|Privacy policy|Modern Slavery Act Transparency Statement|Sitemap|About US| Contact US: help@patsnap.com